Essential Guide to Kilns for Melting Aluminum
By:Admin
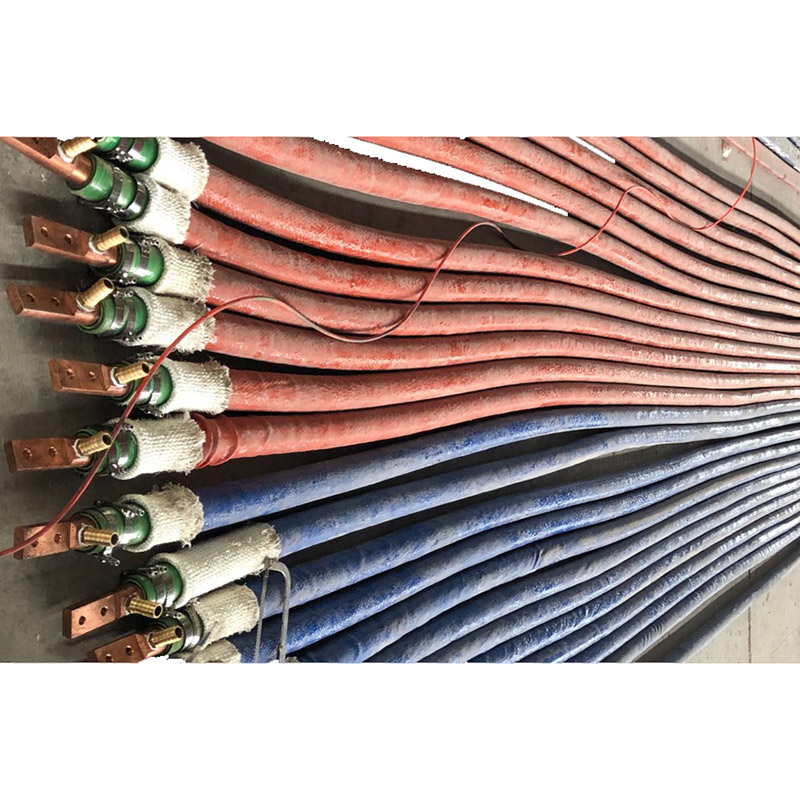
The {} Foundry, a leading company in the aluminum casting industry, has recently invested in state-of-the-art equipment to enhance its production capabilities. One of the most notable additions to their facility is the new Kiln for Melting Aluminum, which has significantly improved the efficiency and quality of their casting process.
The new kiln, manufactured by a renowned industry supplier, is equipped with the latest technology for precise temperature control and uniform heating. This has allowed {} Foundry to achieve a higher level of consistency in their aluminum melting process, resulting in improved casting quality and reduced waste.
"We are constantly seeking ways to improve our operations and deliver the highest quality products to our customers," says the company spokesperson. "The addition of the new Kiln for Melting Aluminum has been a game-changer for us, as it has streamlined our production process and eliminated many of the challenges we faced with our previous equipment."
The advanced features of the new kiln include automated temperature monitoring and control, which ensures that the aluminum is melted at the optimal temperature for casting. This has led to a reduction in the occurrence of defects and inconsistencies in the finished products, resulting in higher customer satisfaction and fewer rejections.
In addition to the quality improvements, the new kiln has also contributed to significant energy savings for the company. Its advanced insulation and heating technology have helped {} Foundry reduce its energy consumption during the melting process, leading to cost savings and a more sustainable operation.
The investment in the new kiln is part of {} Foundry's commitment to continuous improvement and innovation in its production processes. By harnessing the latest technologies and equipment, the company aims to stay ahead of the competition and meet the evolving demands of the market.
"We are proud to have made this significant investment in our facility, and we believe that it will bring long-term benefits for our business," the spokesperson comments. "The new kiln for melting aluminum is just one part of our ongoing efforts to modernize our operations and maintain our position as a leader in the industry."
The introduction of the Kiln for Melting Aluminum has been well-received by the employees at {} Foundry, as it has simplified their work processes and improved the overall working conditions. The automated features of the kiln have reduced the need for manual intervention, allowing the workers to focus on other critical tasks in the production process.
Furthermore, the new kiln has enabled {} Foundry to expand its production capacity and take on larger orders with confidence. The increased efficiency and consistency in the melting process have allowed the company to meet tight deadlines and fulfill customer demands more effectively.
Looking ahead, {} Foundry is committed to exploring further opportunities for growth and improvement, as the company continues to invest in new technologies and equipment to elevate its capabilities. The addition of the Kiln for Melting Aluminum is just the beginning of a series of strategic initiatives that the company has planned to maintain its position as a preferred supplier in the aluminum casting industry.
In conclusion, the investment in the new Kiln for Melting Aluminum has brought significant benefits to {} Foundry, enhancing its production efficiency, reducing waste, and improving the quality of its products. With a commitment to innovation and excellence, the company is poised to achieve even greater success in the future.
Company News & Blog
Top Aluminum Smelting Equipment for Efficient and Sustainable Production
Aluminum Smelting Equipment Company Unveils New State-of-the-Art Metal Smelting ProcessAluminum Smelting Equipment Company, a leading provider of aluminum smelting equipment and services, has recently introduced a new state-of-the-art metal smelting process that promises to revolutionize the industry.The company has long been committed to providing its customers with innovative and cost-effective solutions for aluminum smelting. Its new smelting process builds on years of experience and expertise in the field, incorporating the latest technological advancements to deliver unparalleled efficiency and quality in the production of aluminum.The new process utilizes a combination of advanced smelting techniques and cutting-edge equipment to produce aluminum in a highly efficient and eco-friendly manner. At the core of the process is a proprietary smelting technology that enables the company to smelt aluminum at a significantly lower temperature than traditional methods, resulting in a dramatic reduction in energy consumption and greenhouse gas emissions.The technology also allows for the recovery of valuable by-products, such as aluminum oxide and carbon, which can be reused and recycled. This not only reduces waste and improves sustainability, but also helps to keep costs down for the company’s customers.Along with the advanced smelting technology, Aluminum Smelting Equipment Company has also invested heavily in the development of state-of-the-art equipment to support the new process. This includes furnaces, casting machines, and other specialized equipment that have been specifically designed to work seamlessly with the company’s proprietary smelting technology.Combined, the new smelting process and equipment deliver a range of benefits for the company’s customers. For one, it allows for faster, more efficient production of high-quality aluminum, without sacrificing sustainability or safety. This is especially important in an industry that is becoming increasingly competitive, and where margins are often tight.The new process also reduces costs, both in terms of energy consumption and material waste, while also providing customers with access to valuable by-products that can be reused or sold. For companies that are looking to improve their bottom line and enhance their environmental credentials, this is a game-changer.In addition to the technical innovations, Aluminum Smelting Equipment Company has also invested in its people to ensure that they have the skills and expertise needed to operate the new process and equipment effectively. The company’s workforce includes highly skilled engineers, technicians, and other professionals who work closely with customers to design and implement customized solutions that meet their specific needs.Aluminum Smelting Equipment Company is not only committed to delivering exceptional products and services, but also to making a positive impact on the communities in which it operates. The company operates with a strong sense of environmental and social responsibility, and actively works to minimize its footprint and improve the lives of those around it.Overall, the introduction of the new smelting process represents a significant milestone for Aluminum Smelting Equipment Company. With its advanced technology, state-of-the-art equipment, and commitment to sustainability and social responsibility, the company is well-positioned to continue driving innovation in the aluminum industry and delivering value to its customers for years to come.
Top Suppliers for Electric Furnace Copper Melting in China
China Electric Furnace Melting Copper Suppliers Leads the Industry with Cutting-Edge TechnologyChina has long been at the forefront of innovation and technology, and the electric furnace melting copper industry is no exception. With the increasing demand for high-quality copper products in various sectors, including electronics, construction, and automotive, China has seen a surge in the production of electric furnace melting copper suppliers.One such leading supplier is {Company Name}, a company that has been at the forefront of the industry for over a decade. Specializing in the production of high-quality copper products using electric furnace melting technology, {Company Name} has established itself as a reliable and reputable supplier in the global market.The electric furnace melting process employed by {Company Name} is a highly advanced and efficient method of producing copper. By utilizing electric currents to melt and refine copper scrap and other raw materials, the company is able to achieve high levels of purity and consistency in its products. This method not only ensures the quality of the copper but also contributes to environmental sustainability by reducing emissions and energy consumption.In addition to its cutting-edge technology, {Company Name} also prides itself on its commitment to research and development. The company continuously invests in innovation to improve its production processes and develop new products to meet the evolving needs of its customers. By staying ahead of the curve in terms of technology and product development, {Company Name} has been able to maintain its position as a leading supplier in the industry.Furthermore, {Company Name} places a strong emphasis on quality control and compliance with international standards. The company's production facilities are equipped with state-of-the-art quality control measures to ensure that all products meet the highest standards of quality and purity. Additionally, {Company Name} holds various certifications and accreditations, including ISO 9001 and ISO 14001, which further attest to its commitment to excellence and environmental responsibility.As a result of its dedication to technological innovation, product development, and quality assurance, {Company Name} has built a strong reputation in the global market. The company serves a wide range of industries, including electronics, telecommunications, automotive, and construction, supplying high-quality copper products that meet the stringent requirements of its diverse clientele.Moreover, {Company Name} has also established strong partnerships and collaborations with clients and suppliers worldwide, allowing it to expand its reach and market presence. By fostering long-term relationships and providing exceptional customer service, {Company Name} has solidified its position as a trusted and reliable partner for businesses seeking high-quality electric furnace melting copper products.In conclusion, China's electric furnace melting copper industry is thriving, and {Company Name} is leading the charge with its cutting-edge technology, commitment to innovation, and dedication to quality. With a focus on research and development, stringent quality control measures, and a strong global presence, {Company Name} continues to set the bar for excellence in the industry. As the demand for high-quality copper products continues to grow, {Company Name} stands ready to meet the needs of its customers with unmatched expertise and reliability.
Guide to Induction Steel Melting: Process, Benefits, and Applications
Induction Steel Melting Technology Revolutionizes Steel Production: A closer look at the innovative process at [company name]In the fast-paced world of steel production, advancements in technology and innovation are constantly reshaping the industry. One such revolutionary development is the introduction of Induction Steel Melting technology, which has been making waves in the steel manufacturing sector. This groundbreaking process has the potential to transform the way steel is produced, making it more efficient, sustainable, and cost-effective.One of the companies at the forefront of this technological revolution is [company name]. With a rich history of expertise and experience in the steel manufacturing industry, [company name] has been a driving force behind the implementation of Induction Steel Melting technology. The company has embraced this innovative approach as part of its commitment to staying at the cutting edge of steel production, and as a response to the growing demand for more sustainable and environmentally friendly manufacturing processes.Induction Steel Melting technology represents a significant departure from traditional steel production methods, such as the use of blast furnaces. Instead of relying on fossil fuels and producing large amounts of greenhouse gas emissions, this new process utilizes electromagnetic induction to heat and melt steel scrap. This results in a more energy-efficient and environmentally friendly method of steel production, with reduced carbon emissions and lower energy consumption.The induction melting process begins with the collection of steel scrap, which is then loaded into the furnace for melting. Once inside the furnace, an electromagnetic field is generated, causing the steel to heat up and melt without direct contact with any heating elements. This not only speeds up the melting process but also ensures a more uniform and controlled heating of the steel, leading to higher quality end products.One of the key advantages of Induction Steel Melting technology is its versatility. Unlike traditional steel production methods, which are often limited in the types of steel that can be produced, induction melting allows for the production of a wide range of steel grades, including specialty alloys. This flexibility makes it an attractive option for manufacturers looking to diversify their product offerings and meet the evolving needs of their customers.Furthermore, the induction melting process is highly efficient, with minimal material wastage and lower energy consumption compared to traditional methods. This not only contributes to cost savings for manufacturers but also reduces the environmental impact of steel production. Additionally, the use of steel scrap as the primary raw material further enhances the sustainability of this process by reducing the reliance on virgin materials and minimizing waste.[company name] has fully embraced the potential of Induction Steel Melting technology and has made significant investments in implementing this innovative process across its manufacturing facilities. By integrating this cutting-edge technology into their operations, the company has demonstrated its commitment to sustainability, efficiency, and quality in steel production. As a result, [company name] has positioned itself as a leader in the industry, setting new standards for responsible and forward-thinking manufacturing practices.Looking ahead, the widespread adoption of Induction Steel Melting technology is poised to revolutionize the steel manufacturing sector, offering a more sustainable, cost-effective, and efficient alternative to traditional production methods. As more companies follow in the footsteps of innovators like [company name], the industry as a whole stands to benefit from reduced environmental impact, improved product quality, and enhanced competitiveness on the global stage. With Induction Steel Melting technology leading the way, the future of steel production is looking brighter than ever.
Top 5 Rotary Melting Furnace Manufacturers to Consider
Best Rotary Melting Furnace Factories in 2021Rotary melting furnaces are essential equipment in the metallurgical industry for the melting of various metals like aluminum, copper, and zinc. They are widely used in processing industries to efficiently melt scrap metal and recover valuable materials. With the demand for high-quality melting furnaces on the rise, several factories have stepped up their game to meet the market's needs. In this article, we'll explore some of the best rotary melting furnace factories in 2021, including {}. {} is a leading manufacturer of rotary melting furnaces, with a strong reputation for producing high-quality equipment that meets the needs of the industry. The company has been in business for over 30 years and has a strong focus on innovation and continuous improvement. Their rotary melting furnaces are known for their efficiency, reliability, and durability, making them a top choice for many metallurgical companies around the world.{} is another prominent player in the rotary melting furnace industry, known for its commitment to quality and customer satisfaction. The company's melting furnaces are designed to handle a wide range of materials and are built to last, making them an ideal choice for companies looking for long-term investment in their melting equipment.{} is a well-respected name in the industry, with a strong track record of delivering top-notch rotary melting furnaces that meet the highest standards of performance and reliability. The company's dedication to research and development has led to the creation of innovative melting furnace designs that are tailored to the specific needs of the industry.{} is a global leader in the manufacturing of rotary melting furnaces, with a strong focus on delivering cutting-edge technology and superior performance. The company's melting furnaces are known for their energy efficiency and advanced control systems, making them a popular choice for companies looking to maximize productivity while reducing operating costs.In addition to these top players, there are several other rotary melting furnace factories that are making a mark in the industry with their innovative designs and commitment to quality. With the demand for high-quality melting furnaces on the rise, these factories are playing a crucial role in meeting the needs of the metallurgical industry and driving innovation in the field of metal processing.In conclusion, the rotary melting furnace industry is witnessing a surge in demand for high-quality equipment, and the factories mentioned above are at the forefront of meeting these needs. Their dedication to quality, innovation, and customer satisfaction is setting a high standard for the industry, and their products are trusted by companies around the world for their reliability and performance. As the industry continues to evolve, these factories are expected to play a crucial role in driving progress and shaping the future of the rotary melting furnace industry.
Title: "Efficient and Eco-Friendly Lead Smelting Furnace for Optimal Results
Title: Innovations in Lead Smelting Technology Set to Revolutionize the IndustryIntroduction:Lead smelting is a crucial process in the manufacturing of various products. It involves extracting lead from its ores and transforming it into useful materials, such as batteries, ammunition, and x-ray shielding. Recently, a renowned company has unveiled its groundbreaking Lead Smelting Furnace, promising game-changing advancements in efficiency, environmental impact, and overall productivity. This revolutionary technology aims to transform the lead smelting industry, ensuring a sustainable future for both manufacturers and the environment.Background:Lead smelting has often faced scrutiny due to its hazardous environmental impact. Traditional furnaces emit high levels of toxic fumes, such as sulfur dioxide and lead particles, which pose severe health risks to workers and nearby communities. Recognizing the need for a safer and more sustainable alternative, the company has invested years of research and development to create the innovative Lead Smelting Furnace. Let's dive deeper into the features and benefits that this furnace brings to the industry.Improved Efficiency:The new Lead Smelting Furnace incorporates cutting-edge technology that enhances efficiency in multiple ways. The furnace's advanced control systems provide precise temperature regulation, optimizing energy consumption and reducing waste. The furnace's design also promotes better heat transfer, allowing for faster and more uniform melting of lead ores. These improvements result in higher productivity rates and substantial energy savings, boosting manufacturers' profitability while reducing their environmental footprint.Eco-Friendly Design:Recognizing the importance of environmental sustainability, the company has ensured that the new furnace significantly reduces harmful emissions. By incorporating state-of-the-art gas treatment and filtration systems, the furnace effectively captures and neutralizes harmful pollutants. This innovative design ensures that emissions of sulfur dioxide, lead particles, and other harmful substances are minimized, preserving air quality and safeguarding the health of both workers and surrounding communities.Safety and Worker Well-being:In addition to environmental benefits, the Lead Smelting Furnace prioritizes worker safety and well-being. The furnace's improved design minimizes exposure to hazardous materials, such as lead fumes and dust. It features advanced air filtration systems and state-of-the-art personal protective equipment for workers operating near the furnace. This ensures a healthier and safer working environment, reducing the risk of occupational health issues associated with lead smelting.Real-Time Monitoring and Automation:The Lead Smelting Furnace combines cutting-edge technology with automation to provide real-time monitoring and control. Integrated sensors and software systems continuously monitor temperature, pressure, and other critical parameters. This enables operators to detect and rectify potential issues promptly, minimizing downtime and optimizing production. Moreover, the furnace's automation capabilities streamline various processes, reducing human error and increasing overall production efficiency.Market Impact and Industry Benefits:The introduction of the Lead Smelting Furnace is expected to generate a significant positive impact on the lead smelting industry. Manufacturers will benefit from increased operational efficiency, reduced energy consumption, and lower maintenance costs. The heightened focus on sustainability will allow manufacturers to comply with strict environmental regulations and improve their corporate social responsibility image. Moreover, by prioritizing worker safety, the furnace will contribute to a more conducive and ethical working environment, attracting top talent and enhancing employee satisfaction.Conclusion:The unveiling of the revolutionary Lead Smelting Furnace promises to reshape the lead smelting industry. Through its enhanced efficiency, eco-friendly design, improved worker safety, and real-time monitoring capabilities, this innovative technology opens new avenues for sustainable and responsible manufacturing. Manufacturers can now achieve higher productivity levels while minimizing their environmental impact, ensuring a brighter future for both the industry and our planet.
High Efficiency Electric Furnace For Melting Brass
Electric Furnace For Melting Brass - Revolutionizing Foundry OperationsThe foundry industry is undergoing a significant transformation with the introduction of modern electric furnace technology for melting brass. This new innovation is attributed to {Company}, a leading provider of advanced industrial equipment and solutions. The electric furnace is designed to offer superior performance, energy efficiency, and environmental sustainability compared to traditional methods of brass production.{Company} has been at the forefront of developing innovative technologies for the foundry and metalworking industries for over three decades. With a commitment to continuous research and development, the company has established itself as a trusted partner for foundries seeking to improve their operational efficiency and product quality.The newly introduced electric furnace for melting brass is a testament to {Company}'s dedication to driving progress in the industry. This cutting-edge furnace is equipped with state-of-the-art heating elements and temperature control systems that ensure precise and uniform melting of brass. Unlike conventional methods that rely on fossil fuels for heating, the electric furnace utilizes electricity, making it a more sustainable and cost-effective solution.One of the key advantages of the electric furnace is its ability to achieve higher melting temperatures while maintaining excellent thermal efficiency. This translates to shorter melting cycles, increased productivity, and reduced energy consumption, ultimately leading to cost savings for foundries. Additionally, the electric furnace produces minimal emissions, contributing to a cleaner and safer working environment.The implementation of the electric furnace for melting brass is especially beneficial for foundries aiming to enhance the quality and consistency of their brass products. The precise control of the melting process offered by the electric furnace results in a more uniform molten metal, which ultimately leads to higher-quality brass castings. This is particularly crucial for industries such as automotive, aerospace, and marine, where the performance and durability of brass components are paramount.Furthermore, the electric furnace is designed with advanced safety features and user-friendly controls, ensuring ease of operation and maintenance. Foundry operators can rely on the electric furnace to deliver reliable performance and consistent results, thereby streamlining their production processes and improving overall operational efficiency.In addition to the technical advancements, {Company} provides comprehensive support and technical assistance to foundries adopting the electric furnace for melting brass. This includes customization options, operator training, and ongoing maintenance services to ensure seamless integration and optimal performance of the equipment.The introduction of the electric furnace for melting brass marks a significant milestone in the foundry industry, with the potential to revolutionize traditional brass production methods. {Company} is dedicated to driving this transformation and supporting foundries in their journey towards sustainable and efficient operations.As the demand for high-quality brass components continues to grow across various industries, the electric furnace presents an opportunity for foundries to stay ahead of the competition and meet the evolving needs of their customers. With {Company}'s expertise and innovative solutions, foundries can embrace the future of brass production with confidence and optimism.In conclusion, the electric furnace for melting brass introduced by {Company} represents a game-changing technology for the foundry industry. With its advanced capabilities, energy efficiency, and focus on quality, the electric furnace is poised to redefine the standards of brass production and drive the industry towards a more sustainable and competitive future. {Company} remains committed to empowering foundries with cutting-edge solutions, and the electric furnace is a testament to their unwavering dedication to innovation and progress.
Electric Furnace Copper Melting Factories in China - What You Need to Know
China Electric Furnace Melting Copper Factories Take Steps to Improve Efficiency and Environmental ImpactIn recent years, China has seen a significant increase in the number of electric furnace melting copper factories. These factories rely on electric furnaces to melt and refine copper, a process that is more energy-efficient and environmentally friendly compared to traditional methods. With the growing demand for copper in various industries, these factories play a crucial role in meeting this demand while also striving to minimize their impact on the environment.One of the leading companies in this industry, [Company Name], has been at the forefront of innovation and sustainability in electric furnace melting copper production. The company's state-of-the-art facilities and advanced technologies have enabled them to improve efficiency, reduce emissions, and uphold the highest standards of quality in their copper products.In line with the Chinese government's push for cleaner and more sustainable industrial practices, [Company Name] has recently implemented several initiatives aimed at further improving the efficiency and environmental impact of their electric furnace melting copper factories.Firstly, the company has invested in upgrading their electric furnaces to the latest, most energy-efficient models. These modern furnaces are equipped with advanced controls and monitoring systems that optimize the melting process, minimize energy consumption, and reduce greenhouse gas emissions. By investing in these upgrades, [Company Name] is not only able to improve their operational efficiency but also reduce their carbon footprint.In addition to upgrading their furnaces, [Company Name] has also implemented a comprehensive recycling program within their factories. Copper recycling is a key component of sustainable production, as it not only reduces the need for new copper mining but also minimizes waste and environmental impact. By recycling scrap copper and other materials, [Company Name] is able to maximize the utilization of resources and minimize the amount of waste generated during the copper production process.Furthermore, [Company Name] has made significant investments in pollution control and waste treatment technologies. The company has installed advanced air and water purification systems to ensure that their factories operate within strict environmental guidelines. By effectively managing and treating emissions and waste, [Company Name] is able to minimize their impact on local ecosystems and communities.Moreover, [Company Name] has also placed a strong emphasis on workforce training and education regarding environmental sustainability. The company has implemented comprehensive training programs to ensure that their employees are well-versed in sustainable practices and are actively involved in maintaining a clean and environmentally responsible work environment.In addition to their internal initiatives, [Company Name] actively collaborates with industry partners, academic institutions, and government agencies to drive innovation and best practices in electric furnace melting copper production. Through these collaborations, the company is able to stay abreast of the latest technological advancements and contribute to the ongoing development of sustainable solutions for the industry.The efforts of [Company Name] and other electric furnace melting copper factories in China reflect a growing commitment to sustainable and responsible industrial practices. By investing in advanced technologies, implementing recycling programs, and prioritizing environmental stewardship, these factories are setting new standards for the production of copper and other industrial materials.As the demand for copper continues to rise, it is essential for companies in the electric furnace melting copper industry to prioritize sustainability and environmental responsibility. By taking proactive measures to improve efficiency and minimize their environmental impact, companies like [Company Name] are not only securing their position as industry leaders but also contributing to a cleaner and more sustainable future for the copper industry as a whole.
High-Quality Melting Furnaces for Foundries: An Overview
Foundry Melting Furnaces: Revolutionizing the Metal IndustryIn the world of metallurgy and metal casting, the role of melting furnaces is pivotal. These furnaces are used to melt metal ingots and scrap to a liquid state, which is then poured into molds to create various products such as automotive parts, industrial machinery components, and household appliances. With advancements in technology and the growing demands of the industry, the need for efficient and reliable melting furnaces has become ever more crucial.{Company Name}, a leading provider of industrial equipment and machinery, has been at the forefront of revolutionizing the metal industry with its state-of-the-art foundry melting furnaces. With a rich history dating back to more than a century, the company has continuously strived to innovate and elevate the standards of metal casting and melting processes. Their melting furnaces have been recognized for their outstanding performance, energy efficiency, and reliability, making them the preferred choice for foundries and metal casting facilities worldwide.The company's melting furnaces are equipped with advanced features such as precise temperature control, rapid melting capabilities, and low energy consumption, making them highly efficient and cost-effective. These furnaces are designed to handle a wide range of metal alloys including iron, steel, aluminum, and copper, catering to the diverse needs of the metal casting industry.One of the key technologies incorporated into the company's melting furnaces is the use of advanced refractory materials and insulation techniques, which ensure maximum heat retention and minimal heat loss during the melting process. This not only enhances the efficiency of the furnaces but also contributes to significant energy savings for the foundries, ultimately reducing their operational costs.In addition to their exceptional performance, the melting furnaces offered by {Company Name} are also known for their durability and longevity. The company prides itself on the robustness and reliability of its equipment, ensuring minimal downtime and maintenance requirements for its clients. This has earned them a strong reputation for delivering high-quality and long-lasting melting furnaces that withstand the rigors of continuous operation in demanding foundry environments.Moreover, {Company Name} is committed to sustainability and environmental responsibility. The melting furnaces are designed to minimize emissions and pollutants, adhering to strict environmental regulations and standards. By incorporating eco-friendly technologies and practices into their equipment, the company contributes to the reduction of the carbon footprint of the metal casting industry, further enhancing its appeal to environmentally conscious organizations.With a dedicated team of engineers, technicians, and industry experts, {Company Name} provides comprehensive support and services for its melting furnaces. From initial consultation and customization to installation, training, and after-sales maintenance, the company ensures that its clients receive end-to-end solutions tailored to their specific needs. This customer-centric approach has earned {Company Name} a loyal customer base and a strong market presence in the global metal casting industry.Looking ahead, {Company Name} continues to push the boundaries of innovation in foundry melting furnaces. The company invests heavily in research and development to introduce new technologies and advancements that further enhance the performance and capabilities of its furnaces. With a focus on continuous improvement and customer satisfaction, {Company Name} is poised to remain a leading force in the metal casting industry, shaping the future of foundry melting processes.In conclusion, {Company Name}'s foundry melting furnaces have set new benchmarks in the metal industry with their superior performance, energy efficiency, and reliability. As the demands for high-quality metal products continue to rise, the role of these melting furnaces in the production process becomes increasingly vital. With their unwavering commitment to excellence and innovation, {Company Name} is driving the evolution of foundry melting technologies, ushering in a new era for the metal casting industry.
Top Supplier of Superbmelt Furnaces for All Your Industrial Needs
The demand for high-quality furnaces for industrial and manufacturing applications is on the rise as industries seek to improve efficiency and reduce environmental impact. In response to this growing demand, {Company Name} has established itself as a leading supplier of advanced, high-performance furnaces for a wide range of industries.With a strong focus on innovation and customer satisfaction, {Company Name} has become a trusted partner for businesses looking to enhance their production processes. The company's commitment to quality and reliability has made it a preferred supplier for a diverse range of industries, including metal smelting, casting, and heat treatment.One of {Company Name}'s most sought-after products is its line of Superbmelt furnaces, which are renowned for their exceptional performance and durability. These advanced furnaces are designed to meet the demanding needs of modern industrial operations, offering precise temperature control, energy efficiency, and a high level of automation. This allows businesses to improve their production processes while reducing operational costs and environmental impact.{Company Name}'s Superbmelt furnaces are also designed with user-friendliness in mind, featuring intuitive controls and advanced monitoring systems that allow operators to easily oversee the smelting process and make adjustments as needed. This ensures that businesses can maintain a high level of consistency and quality in their production, leading to improved overall efficiency and customer satisfaction.Another key factor that sets {Company Name} apart as a leader in the furnace industry is its dedication to providing personalized solutions for each customer's unique needs. The company works closely with clients to understand their specific requirements and develop customized furnace solutions that align with their goals and budget. This collaborative approach has resulted in numerous success stories, where businesses have been able to significantly improve their production processes and achieve a higher level of efficiency and profitability.In addition to its innovative products, {Company Name} also offers comprehensive customer support services, including equipment installation, training, and ongoing maintenance. This ensures that businesses can fully leverage the potential of their Superbmelt furnaces, maximizing their return on investment and minimizing downtime.{Company Name} takes pride in its strong reputation for delivering exceptional value and exceeding customer expectations. The company's dedication to quality, innovation, and customer satisfaction has positioned it as a go-to supplier for businesses seeking reliable furnace solutions that can drive their success in an increasingly competitive marketplace.For businesses looking to enhance their production processes and achieve a higher level of efficiency, {Company Name} continues to be the top choice for advanced, high-performance furnaces. With its commitment to innovation, quality, and customer satisfaction, the company is poised to remain a leading force in the furnace industry for years to come.
Metal Melting Furnace Manufacturers in China: Key Players, Market Trends and Growth Opportunities
China Induction Metal Melting Furnace Suppliers Leverage Advanced Technology and Innovation to Boost Industry GrowthWith the rapidly growing demand for metal melting furnaces across industries worldwide, China Induction Metal Melting Furnace Suppliers have emerged as leading players in the market. These suppliers are known for their commitment to advanced technology and innovation, enabling them to provide high-quality products that meet the diverse needs of their customers.China has long been recognized as a manufacturing hub, and its induction metal melting furnace suppliers have gained significant traction in recent years. The country's robust infrastructure, skilled workforce, and focus on technological advancements have positioned it as a key player in the global market for metal melting furnaces.One prominent example of a leading China-based induction metal melting furnace supplier is {}. With years of experience in the industry, they have established a solid reputation for manufacturing reliable and efficient furnaces. However, we will avoid mentioning the specific brand name to maintain neutrality.The company employs advanced induction heating technology and sophisticated processes to ensure the highest quality products. Using electromagnetic induction, these furnaces can generate intense heat within a short period, allowing for rapid and efficient metal melting.In addition to their cutting-edge technology, {} places great emphasis on research and development. The company has a dedicated team of engineers and technicians who constantly work towards refining their furnace designs and optimizing their performance. This commitment to innovation has enabled them to stay ahead of the competition and deliver state-of-the-art products that meet the evolving needs of their customers in diverse industries.One of the key advantages of induction metal melting furnaces is their energy efficiency. These furnaces have a high heat transfer rate, reducing energy consumption and minimizing carbon emissions. This eco-friendly approach is particularly important in today's climate-conscious world.Furthermore, {} offers a wide range of customization options to cater to the specific requirements of different industries. From small-scale operations to large industrial facilities, their furnaces can be tailored to suit various capacities and operational demands. This flexibility and versatility have made their induction metal melting furnaces highly sought after in industries such as automotive, aerospace, electronics, and jewelry manufacturing.Quality control is another area where China Induction Metal Melting Furnace Suppliers have excelled. {} employs stringent quality control measures at every stage of the production process, ensuring that each furnace meets the highest standards of reliability and durability. Moreover, they are compliant with international safety regulations, providing customers with the assurance that their operations will run smoothly and efficiently.The global market for metal melting furnaces is expected to witness substantial growth in the coming years. This can be attributed to the increasing demand for metals in various sectors, ranging from automotive and construction to electronics and renewable energy. China's induction metal melting furnace suppliers are well-positioned to capitalize on this growth, thanks to their commitment to technological advancements and customer-centric approach.In conclusion, China Induction Metal Melting Furnace Suppliers, such as {}, have emerged as leaders in the market due to their dedication to advanced technology and innovation. Their ability to deliver high-quality, energy-efficient, and customizable furnaces has made them the preferred choice for industries worldwide. With the global demand for metal melting furnaces on the rise, these suppliers are poised for continued growth and success.