Top Kiln Supplier for Aluminum Melting in China
By:Admin
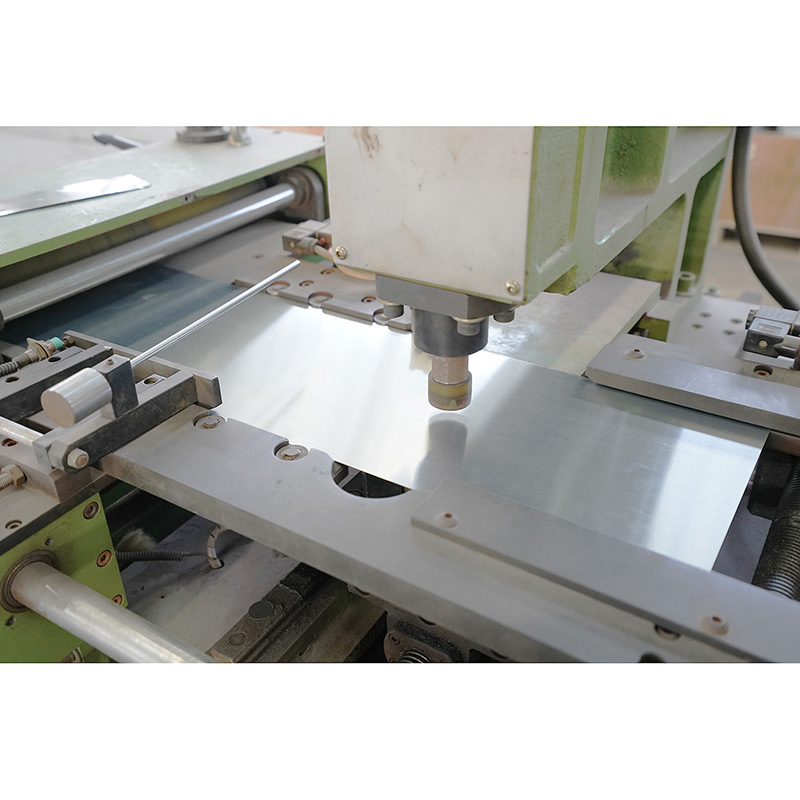
The new kiln is designed to provide a more efficient and sustainable way to melt aluminum, offering significant improvements in energy consumption and environmental impact. It is equipped with state-of-the-art technology that allows for precise control over the melting process, resulting in higher quality aluminum with reduced impurities.
In addition to its advanced technology, the new kiln boasts a higher capacity and faster melting speed, allowing for increased productivity and reduced downtime. This is a significant advantage for aluminum manufacturers, as it helps to streamline their production processes and meet the growing demand for high-quality aluminum products.
"We are thrilled to introduce our new kiln for melting aluminum," said a spokesperson for China Kiln To Melt Aluminum Supplier. "We are committed to providing our customers with the most advanced and efficient solutions for their aluminum melting needs, and we believe that this new kiln will set a new standard in the industry."
The company's dedication to innovation and customer satisfaction is reflected in their long-standing reputation as a trusted supplier of kilns for the aluminum industry. With a track record of delivering high-quality products and exceptional customer service, they have established themselves as a leader in the market.
The introduction of the new kiln is expected to further strengthen the company's position in the industry, as it demonstrates their ongoing commitment to advancing technology and providing top-of-the-line solutions for their customers. It also reflects their dedication to sustainability, as the new kiln is designed to minimize energy consumption and reduce environmental impact.
"We understand the importance of sustainability in today's industry, and we are proud to offer a solution that not only improves efficiency and productivity but also reduces our environmental footprint," the spokesperson added. "We believe that this new kiln will benefit both our customers and the environment, and we are excited to see the positive impact it will have on the industry."
China Kiln To Melt Aluminum Supplier is known for its comprehensive range of kilns and furnaces for the aluminum industry, offering tailored solutions to meet their customers' specific needs. From melting and holding to heat treatment and recycling, the company's products are designed to deliver exceptional performance and reliability.
The introduction of the new kiln is a testament to the company's ongoing commitment to innovation and excellence, as well as their drive to provide cutting-edge solutions for the aluminum industry. With their proven track record and dedication to customer satisfaction, China Kiln To Melt Aluminum Supplier is well-positioned to continue leading the market with their advanced kiln technology.
Company News & Blog
Title: "Efficient and Eco-Friendly Lead Smelting Furnace for Optimal Results
Title: Innovations in Lead Smelting Technology Set to Revolutionize the IndustryIntroduction:Lead smelting is a crucial process in the manufacturing of various products. It involves extracting lead from its ores and transforming it into useful materials, such as batteries, ammunition, and x-ray shielding. Recently, a renowned company has unveiled its groundbreaking Lead Smelting Furnace, promising game-changing advancements in efficiency, environmental impact, and overall productivity. This revolutionary technology aims to transform the lead smelting industry, ensuring a sustainable future for both manufacturers and the environment.Background:Lead smelting has often faced scrutiny due to its hazardous environmental impact. Traditional furnaces emit high levels of toxic fumes, such as sulfur dioxide and lead particles, which pose severe health risks to workers and nearby communities. Recognizing the need for a safer and more sustainable alternative, the company has invested years of research and development to create the innovative Lead Smelting Furnace. Let's dive deeper into the features and benefits that this furnace brings to the industry.Improved Efficiency:The new Lead Smelting Furnace incorporates cutting-edge technology that enhances efficiency in multiple ways. The furnace's advanced control systems provide precise temperature regulation, optimizing energy consumption and reducing waste. The furnace's design also promotes better heat transfer, allowing for faster and more uniform melting of lead ores. These improvements result in higher productivity rates and substantial energy savings, boosting manufacturers' profitability while reducing their environmental footprint.Eco-Friendly Design:Recognizing the importance of environmental sustainability, the company has ensured that the new furnace significantly reduces harmful emissions. By incorporating state-of-the-art gas treatment and filtration systems, the furnace effectively captures and neutralizes harmful pollutants. This innovative design ensures that emissions of sulfur dioxide, lead particles, and other harmful substances are minimized, preserving air quality and safeguarding the health of both workers and surrounding communities.Safety and Worker Well-being:In addition to environmental benefits, the Lead Smelting Furnace prioritizes worker safety and well-being. The furnace's improved design minimizes exposure to hazardous materials, such as lead fumes and dust. It features advanced air filtration systems and state-of-the-art personal protective equipment for workers operating near the furnace. This ensures a healthier and safer working environment, reducing the risk of occupational health issues associated with lead smelting.Real-Time Monitoring and Automation:The Lead Smelting Furnace combines cutting-edge technology with automation to provide real-time monitoring and control. Integrated sensors and software systems continuously monitor temperature, pressure, and other critical parameters. This enables operators to detect and rectify potential issues promptly, minimizing downtime and optimizing production. Moreover, the furnace's automation capabilities streamline various processes, reducing human error and increasing overall production efficiency.Market Impact and Industry Benefits:The introduction of the Lead Smelting Furnace is expected to generate a significant positive impact on the lead smelting industry. Manufacturers will benefit from increased operational efficiency, reduced energy consumption, and lower maintenance costs. The heightened focus on sustainability will allow manufacturers to comply with strict environmental regulations and improve their corporate social responsibility image. Moreover, by prioritizing worker safety, the furnace will contribute to a more conducive and ethical working environment, attracting top talent and enhancing employee satisfaction.Conclusion:The unveiling of the revolutionary Lead Smelting Furnace promises to reshape the lead smelting industry. Through its enhanced efficiency, eco-friendly design, improved worker safety, and real-time monitoring capabilities, this innovative technology opens new avenues for sustainable and responsible manufacturing. Manufacturers can now achieve higher productivity levels while minimizing their environmental impact, ensuring a brighter future for both the industry and our planet.
Top Supplier of Induction Copper Melting Furnaces in China
In the world of metallurgy and metal processing, copper is one of the most widely used metals. Its versatility, electrical conductivity, and durability make it an ideal material for a wide range of applications. The demand for copper is high, and with it comes the need for reliable and efficient copper melting furnaces.Enter China Induction Copper Melting Furnace Supplier (CICMF), a leading manufacturer of induction copper melting furnaces. Established in 1984, CICMF has been providing high-quality furnaces to clients all over the world. With over three decades of experience in the industry, the company prides itself on its commitment to innovation, reliability, and customer satisfaction.CICMF offers a variety of induction copper melting furnaces, each uniquely designed to meet the specific needs of its clients. From small-scale operations to large commercial applications, CICMF has a furnace that can cater to any melting requirement. The company's range of furnaces includes tilting type induction melting furnaces, stationary type induction melting furnaces, and vacuum induction melting furnaces.The company's tilting type induction melting furnace is a popular choice for small to medium-sized melting operations. It offers efficient, fast, and safe heating that can help clients improve their productivity and profitability. The furnace is easy to operate and maintain, making it an ideal choice for both experienced and beginner operators. It also features a tilting mechanism that allows for easy pouring and a more convenient emptying process.CICMF's stationary type induction melting furnace, on the other hand, is designed for larger melting operations. It offers the same level of efficiency and reliability as the tilting furnace, but with a larger capacity. One of its unique features is its ability to melt a variety of metals, including copper, aluminum, and zinc.CICMF's vacuum induction melting furnace is ideal for clients who need to produce high-quality and high-purity copper alloys. The furnace can achieve high vacuum and low-pressure conditions, which are essential in producing high-purity alloys. The furnace is controlled by an advanced computer system that allows for strict temperature control and melting through different stages. It also features a tilting mechanism for easy pouring and a fully automated process.Over the years, CICMF has established itself as a trusted supplier of induction copper melting furnaces. The company's commitment to quality and innovation has earned the trust and loyalty of its clients. Its furnaces are used by a wide range of industries, including automobile manufacturing, electronics, and construction.Aside from its high-quality furnaces, CICMF also offers technical support, training, and after-sales services to its clients. Its team of experienced engineers and technicians is always ready to provide assistance, from installation to maintenance. The company also offers spare parts and components to ensure its clients' equipment is always up and running.In conclusion, China Induction Copper Melting Furnace Supplier is a leading manufacturer of induction copper melting furnaces that have gained a reputation for quality, reliability, and efficiency. Its range of furnaces caters to the specific needs of its clients, and its commitment to innovation continues to drive its success in the industry. With its experienced team, technical support, and after-sales services, CICMF is more than just a supplier of equipment – it is a partner to its clients, helping them achieve their goals and grow their businesses.
Groundbreaking Discovery Unveils New Potential in Foundry Induction Technology
Title: Revolutionary Induction Technology Poised to Revamp Foundry IndustryIntroduction:In today's rapidly advancing industrial landscape, innovation and technological advancements continue to redefine manufacturing processes across various sectors. In line with this trend, a groundbreaking technology has emerged in the foundry industry, promising unprecedented efficiencies and environmental benefits. This revolutionary induction technology, developed and commercialized by a pioneering industry leader, is set to transform the landscape of foundry operations worldwide.Background:The foundry industry has traditionally relied heavily on fossil fuel-powered furnaces to melt metal alloys for casting processes. Though effective, these traditional methods are environmentally taxing, generating significant greenhouse gas emissions and consuming large quantities of non-renewable resources. With growing concerns over climate change and sustainability, there has been a pressing need for forward-thinking solutions that address these issues without sacrificing operational efficiency.Induction Technology: A Paradigm ShiftEnter the groundbreaking induction technology, a transformative breakthrough that promises to redefine the foundry sector. The technology enables the melting of metal alloys through electromagnetic induction, rather than relying on conventional fossil fuel heating sources. This process significantly reduces the carbon footprint of the foundry industry, making it more sustainable and environmentally friendly.Induction Foundry: Leader in Revolutionizing Casting ProcessesOne prominent industry player at the forefront of this transformation is Induction Foundry (name removed). As a leading innovator and manufacturer of induction equipment, the company has played a pivotal role in driving the adoption of this game-changing technology. By combining expertise in metallurgy, engineering, and sustainable practices, Induction Foundry has introduced a range of highly efficient induction furnaces and equipment that have garnered worldwide acclaim.Increased Efficiency and Cost SavingsInduction Foundry's cutting-edge induction furnaces boast several advantages over conventional melting techniques. Firstly, the technology offers unparalleled energy efficiency, significantly reducing operating costs compared to traditional furnaces. Induction furnaces achieve optimal melting temperatures faster, resulting in shorter cycle times, increased productivity, and reduced energy consumption. The electromagnetic induction process also allows more precise temperature control, ensuring consistent casting quality and minimizing material waste.Environmental Sustainability at the CoreInduction Foundry's environmentally conscious equipment aligns well with the global sustainability movement. By eliminating fossil fuel combustion, the company's induction furnaces minimize emissions, improve air quality, and help combat climate change. Additionally, the induction process generates significantly less waste compared to traditional methods, as it avoids the need for refractory materials. These sustainable features have positioned Induction Foundry as a responsible industry leader, garnering acclaim and recognition from environmental organizations.A Future-Proofed Foundry IndustryWith environmental regulations becoming increasingly stringent and consumers demanding products manufactured through sustainable processes, the foundry industry must adapt rapidly. Induction technology offers the perfect solution - a highly efficient, sustainable, and cost-effective alternative to conventional melting processes. By embracing induction technology, foundry operators can modernize their facilities, enhance operational efficiency, and gain a competitive edge in the market.Global Adoption and Growth PotentialInduction Foundry's induction furnaces have witnessed substantial adoption across the globe. Foundries in various industries, such as automotive, aerospace, and machinery manufacturing, have implemented this transformational technology. The positive feedback and success stories from early adopters have further accelerated the growth potential of the induction foundry industry.Conclusion:As the global focus on sustainability intensifies, the foundry industry must embrace new and innovative technologies to stay ahead of the curve. Induction Foundry's pioneering induction technology presents a transformative opportunity for foundries worldwide to enhance productivity, reduce costs, and minimize environmental impact. With a growing customer base, Induction Foundry's induction furnaces are setting new benchmarks for the foundry industry while paving the way for a more sustainable future.
New Electric Crucible Introduces Revolutionary Technology for Efficient Melting" --> "Revolutionary Technology for Efficient Melting Unveiled with Electric Crucible
Title: Pioneering Electric Crucible Transforms the Manufacturing IndustryIntroduction: In a groundbreaking development, an innovative electric crucible has emerged, offering a cutting-edge solution for the manufacturing industry. With its advanced technology and groundbreaking features, this electric crucible, developed by a leading materials research company, promises to revolutionize manufacturing processes, enabling greater efficiency, sustainability, and precision. Electric Crucible: Redefining Manufacturing The newly unveiled electric crucible is poised to redefine manufacturing by offering an unparalleled level of control and flexibility. Traditionally, metal casting and materials processing have heavily relied on fossil fuel-powered crucibles, resulting in significant environmental impacts and limited precision. However, this pioneering electric crucible brings forth multiple advancements poised to overcome these challenges.Sustainable Manufacturing with Lower Environmental ImpactOne of the most significant advantages of adopting this electric crucible technology is its reduced environmental impact. By eliminating the need for fossil fuel combustion, the electric crucible drastically reduces greenhouse gas emissions, contributing to a cleaner and more sustainable manufacturing process. This exciting development comes at a time when industries worldwide are exploring sustainable practices, making this electric crucible the prime choice for environmentally-conscious manufacturers.Enhanced Precision and EfficiencyIn addition to its environmental benefits, the electric crucible also offers unparalleled precision and efficiency. The technology harnesses state-of-the-art heating elements and computer-controlled systems, allowing manufacturers to achieve a higher level of precision in temperature control. This precise control over temperature ensures consistent and uniform heating, minimizing material waste and increasing overall manufacturing efficiency. Furthermore, the electric crucible's design allows for swift and accurate changes in production volume, making it ideal for industries with rapidly changing demands.Real-Time Monitoring and Safety FeaturesAccompanying its advanced heating technology, the electric crucible also includes real-time monitoring capabilities and cutting-edge safety features. These additional features ensure optimal performance and safeguard against potential accidents. The real-time monitoring system provides continuous updates on temperature, pressure, and other crucial parameters, enabling manufacturers to maintain process control and make necessary adjustments when required. Furthermore, the electric crucible includes built-in safety measures to prevent overheating or material spillage, reducing the risk of accidents and enhancing overall workplace safety.Smart Integration and CompatibilityApart from its innovative features, the electric crucible can seamlessly integrate with existing manufacturing systems. Its compatibility with various production lines and automation solutions ensures a hassle-free adoption process for manufacturers. By eliminating the need for a complete overhaul of manufacturing infrastructure, this crucible minimizes downtime and reduces implementation costs, garnering significant interest from industry leaders.Future Prospects and Industry ImplicationsThe introduction of the electric crucible marks a significant milestone in the manufacturing industry, unlocking a myriad of possibilities for future advancements. With greater precision, enhanced energy efficiency, and reduced environmental impact, manufacturers can achieve higher productivity levels while prioritizing sustainability. Furthermore, this crucible's compatibility with automation solutions paves the way for increased integration of Industry 4.0 technologies, boosting overall manufacturing efficiency and competitiveness.ConclusionThe unveiling of the electric crucible signifies a paradigm shift in the manufacturing industry, providing a transformative solution that combines sustainability, efficiency, and precision. With its cutting-edge technology, reduced environmental impact, and seamless integration capabilities, this pioneering innovation promises to reshape manufacturing processes and propel industries towards a more sustainable future. As manufacturers embrace the electric crucible, a new era of enhanced manufacturing awaits, revolutionizing the production landscape across the globe.
Top-rated Furnace Factories for High-Quality Melting Solutions
In recent years, there has been an increasing demand for high-quality melting and casting equipment across various industries. As a result, the search for a reliable and efficient furnace manufacturer has become a top priority for many organizations. While there are numerous brands in the market, the Best Superbmelt Furnace Factories have stood out from the rest.The Best Superbmelt Furnace Factories have been in operation for over two decades, providing innovative solutions for metal melting and casting. With a team of experienced engineers and designers, the company has developed state-of-the-art equipment that meets the diverse needs of its customers. Their broad range of furnaces includes induction melting furnaces, arc melting furnaces, smelting furnaces, and vacuum melting furnaces.The company's success can be attributed to its commitment to quality and exceptional customer service. Best Superbmelt Furnace Factories use high-quality materials and components to ensure that their machines are of the highest standard. Additionally, their machines are designed with user experience in mind, making them easy to operate and maintain.One of the key features of the Best Superbmelt Furnace Factories furnaces is their energy efficiency. These machines have been designed to minimize energy consumption while maintaining peak performance. By using advanced technology, the company has developed furnaces that reduce energy costs and contribute to a cleaner environment.Another significant advantage of Best Superbmelt Furnace Factories furnaces is their adaptability. The company provides customized machines that meet the specific requirements of clients. Whether the need is for small-scale melting or large-scale industrial applications, the company can design and manufacture furnaces that meet the client's needs.In addition to providing excellent machines, Best Superbmelt Furnace Factories also offer exceptional customer service. The company's team of experts is always available to provide technical support to ensure that clients' machines are operating optimally. Additionally, the company offers training programs to help clients operate their machines safely and efficiently.Over the years, Best Superbmelt Furnace Factories have established a reputation as a trusted and reliable furnace manufacturer. Their machines have been widely used in various industries, including foundries, jewelry making, aerospace, and automotive. The company has an international presence and has served clients from different parts of the world.In conclusion, the Best Superbmelt Furnace Factories have become a household name in the melting and casting industry. Their commitment to quality, exceptional customer service, energy efficiency, adaptability, and innovation has set them apart from the competition. With their exceptional machines and unparalleled customer service, Best Superbmelt Furnace Factories is the go-to company for all melting and casting needs.
Top Zinc Melting Furnace Factories: Discover the Best Manufacturers in the Industry
Title: Advancements in Zinc Melting Furnace Technology Revolutionize the IndustryIntroduction:Zinc melting furnace factories play a crucial role in the manufacturing process of various industries, including automotive, construction, and electronics. These factories are responsible for melting and refining zinc to its molten form, which is then used for various applications. With technological advancements, several manufacturers have made significant strides in improving these furnaces' efficiency, safety, and environmental impact. In this article, we explore the recent developments in zinc melting furnace technology and their impact on the industry.1. Enhanced Efficiency through Innovative Designs:Leading zinc melting furnace manufacturers have been focusing on improving efficiency to meet the growing demands of zinc-consuming industries. They have developed advanced designs that optimize heat transfer, resulting in faster and more efficient melting processes. These innovative designs utilize various methods such as induction heating, electric resistive heating, or fossil fuel combustion to achieve optimal melting conditions.Furthermore, precise temperature control mechanisms and advanced insulation materials have been integrated into these furnaces, minimizing heat loss and enabling uniform melting throughout the entire process. As a result, manufacturers can achieve higher throughput capacities while reducing energy consumption, ultimately leading to cost savings and increased productivity.2. Emphasis on Safety Measures:Ensuring worker safety is of utmost importance in zinc melting furnace factories. Recent advancements have brought forth enhanced safety features, making the operating environment safer for workers. Furnaces now come equipped with sensor-based systems that continuously monitor various parameters like temperature, pressure, and gas leakage. In the event of any abnormalities or hazardous situations, these systems can automatically shut down the furnace or trigger alarms, thereby preventing accidents and ensuring a secure work environment.Moreover, improved ventilation and exhaust systems have been implemented to minimize the health risks associated with exposure to metal fumes and other harmful byproducts generated during the melting process. These advancements have significantly reduced the health hazards for workers, leading to improved overall well-being and better work conditions.3. Environmental Sustainability:Zinc melting furnace factories have made notable progress in reducing their environmental footprint. Manufacturers have adopted cleaner and more sustainable energy sources, such as electricity from renewable sources or use of cleaner fuels like natural gas, minimizing greenhouse gas emissions. Additionally, advanced filtration systems have been introduced to capture and treat harmful byproducts like particulate matter, sulfur dioxide, and nitrogen oxides generated during the melting process.Furthermore, recycling initiatives have gained momentum, allowing for the recycling and reuse of zinc scrap and dross generated during the manufacturing process. This significantly reduces waste disposal, conserves natural resources, and promotes a circular economy approach.Conclusion:Recent advancements in zinc melting furnace technology have revolutionized the industry, bringing forth numerous benefits such as enhanced efficiency, improved safety measures, and a reduced environmental impact. The integration of innovative designs, refined temperature control mechanisms, and advanced safety features have enabled manufacturers to achieve higher productivity while safeguarding the well-being of workers. Moreover, the adoption of sustainable practices, including the use of cleaner energy sources and recycling initiatives, have promoted environmental sustainability within the industry.As the demand for zinc in various industries continues to grow, it is encouraging to witness the continuous efforts made by zinc melting furnace factories to push the boundaries of technological innovation. These advancements not only contribute to the industry's growth but also address the pressing concerns of efficiency, safety, and sustainability.
The Importance of Selecting a High-Quality Furnace Manufacturer for Efficient Metal Smelting
Title: Revolutionary Industrial Furnace Manufacturer Introduces Cutting-Edge Technology for Enhanced Metal Melting Processes Introduction: In the ever-evolving landscape of industrial manufacturing, the need for efficient and eco-friendly metal melting processes has become paramount. Enter the pioneering furnace manufacturer, renowned for its ground-breaking innovations and unwavering commitment to quality and customer satisfaction. This revolutionary company, distinguished for its unmatched research and development capabilities, is set to revolutionize metal melting through its state-of-the-art technology.Revolutionizing Metal Melting Processes:With a rich history of exceeding industry expectations, this visionary furnace manufacturer has left an indelible mark on the global manufacturing landscape. By leveraging a deep understanding of user requirements and utilizing cutting-edge technology, they have successfully developed an array of furnaces with unrivaled capabilities.One of the most prominent achievements of this manufacturer is the development of their advanced induction heating technology. This groundbreaking technology harnesses the power of electromagnetic induction to efficiently melt a wide range of metals. With remarkable precision, these induction furnaces can melt and heat metals within seconds, significantly reducing production time and optimizing throughput. Moreover, this energy-efficient technology ensures minimal waste, making it an environmentally friendly solution.Committed to customer satisfaction, this manufacturer strives to offer versatility in their product lineup. Understanding the diversity of metal melting requirements across industries, they have meticulously designed a range of furnaces catering to different needs. From small-scale melting furnaces for laboratory purposes to large-scale industrial furnaces for mass production, this manufacturer offers tailored solutions to meet specific demands.Moreover, this furnace manufacturer's commitment to innovation is evident in their incorporation of the latest automation technologies into their products. Advanced features such as temperature control systems, automatic feeding mechanisms, and real-time monitoring capabilities enhance both productivity and safety. Such technological advancements streamline operations by minimizing human intervention and ensuring precise control over the metal melting process.The manufacturer's unwavering dedication to quality and reliability is exemplified by their stringent quality control measures. Every furnace undergoes rigorous testing protocols, ensuring that only products of the highest standards reach the market. By conforming to international quality certifications, this manufacturer assures their customers of the durability and longevity of their products.Furthermore, this forward-thinking furnace manufacturer recognizes the importance of comprehensive after-sales support. Their team of skilled technicians and engineers offers prompt assistance for installation, maintenance, and troubleshooting. This commitment to customer care ensures that the benefits of their cutting-edge technology are fully realized by their clients, ultimately driving productive and efficient metal melting processes.Expanding Global Footprint:This esteemed furnace manufacturer's relentless pursuit of excellence has propelled them to establish a robust global presence. With an extensive distribution network and strategic partnerships, they have successfully catered to the evolving demands of industries worldwide. By offering not just superior products, but also impeccable customer service, this manufacturer has consistently outperformed competitors, securing a trusted position in the market.Conclusion:In a fiercely competitive industrial landscape, distinguished by constant technological advancements, this revolutionary furnace manufacturer stands tall as a leading provider of innovative metal melting solutions. Guided by their unwavering commitment to quality, customer satisfaction, and environmental responsibility, they continue to redefine industry standards in terms of efficiency, reliability, and precision. With their cutting-edge technology and comprehensive after-sales support, industries across the globe can look forward to enhanced metal melting processes and streamlined production, powered by the products of this visionary manufacturer.
Leading Furnace Manufacturers in China Offer Professional Melting Solutions for Various Industries
Title: Leading Furnace Manufacturer in China Sets New Industry Benchmark with Cutting-Edge TechnologyIntroduction:As the global demand for advanced industrial furnaces continues to rise, China has emerged as a leading producer and exporter of top-of-the-line furnace equipment. In line with this trend, one prominent player in the industry, henceforth referred to as China Superbmelt Furnace Manufacturers, has been making waves with its innovative and high-performance furnace solutions. With an aim to revolutionize the metal casting and smelting industry, China Superbmelt has firmly established itself as an industry frontrunner through its relentless pursuit of excellence.Delivering Cutting-Edge Furnace Solutions:China Superbmelt Furnace Manufacturers has gained an unparalleled reputation due to its commitment to utilizing the most advanced technologies in metal smelting and casting processes. Armed with an in-depth understanding of customer requirements and a dedication to engineering excellence, the company offers an extensive range of furnace solutions catering to diverse industries. From small-scale applications to large-scale industrial operations, their furnaces are designed to optimize energy efficiency, precision control, and productivity.The company specializes in manufacturing high-quality electric heating furnaces, induction melting furnaces, resistance heating furnaces, and more. These state-of-the-art furnaces are capable of handling various materials, including precious metals, iron, steel, aluminum, copper, and alloys, ensuring versatility across multiple sectors such as jewelry manufacturing, metal recycling, automotive, aerospace, and electronics.Unparalleled Technological Advancements:China Superbmelt prides itself on its relentless pursuit of innovation, consistently pushing boundaries to develop cutting-edge technologies that set new industry benchmarks. The company has devoted substantial resources to the research and development of its furnace systems, resulting in technologically enhanced products that provide precise temperature control, high energy efficiency, and significantly reduced environmental impact.One of China Superbmelt's notable advancements is its integration of artificial intelligence (AI) into its furnace systems. By incorporating machine learning algorithms and real-time data analysis, their intelligent furnaces are capable of optimizing energy consumption, improving melting efficiency, and reducing waste. This breakthrough technology positions China Superbmelt at the forefront of the industry, allowing them to offer their customers unparalleled productivity gains and cost efficiencies.International Recognition and Commitment to Quality:China Superbmelt's commitment to quality and excellence has earned the company widespread recognition both domestically and internationally. With a strong emphasis on research and development, the company's expert engineers are consistently working towards enhancing furnace performance, reliability, and safety.Furthermore, China Superbmelt adheres to rigorous quality control standards, ensuring that each furnace undergoes comprehensive testing and inspection before reaching the market. This dedication to quality has earned them various certifications and accolades, further solidifying their position as a trusted supplier of furnace equipment worldwide.Global Footprint and Customer Success:Driven by its unwavering commitment to customer satisfaction, China Superbmelt has successfully expanded its presence to over 80 countries, with a strong customer base that continues to grow. By offering customized furnace solutions tailored to meet specific industry requirements, the company has built lasting partnerships with numerous clients, including small businesses, large enterprises, and government institutions alike.China Superbmelt's holistic approach doesn't end with providing top-of-the-line furnace systems; they also offer comprehensive technical support, after-sales service, and training programs. This commitment to long-term customer success has garnered them enthusiastic testimonials from satisfied clients, who praise the company for its prompt responsiveness and dedication to problem-solving.Conclusion:China Superbmelt Furnace Manufacturers has firmly positioned itself as a global leader in the production of cutting-edge furnace technology, setting new industry standards through its commitment to innovation, quality, and customer satisfaction. With a dedicated team of experts and an unwavering focus on R&D, the company is poised to continue its growth trajectory and shape the future of the furnace manufacturing industry.
Melting Induction Furnaces: Efficient Iron Melting Solutions
Iron Melting Induction Furnace Revolutionizes the Foundry IndustryThe foundry industry is an essential part of the global manufacturing sector, providing metal castings for a variety of industries, including automotive, aerospace, and construction. Iron is one of the most commonly used metals in this sector, and its melting is a crucial step in the casting process. Traditionally, iron melting has been done using fossil fuel-fired cupolas, which have significant environmental and health risks. However, thanks to the power of innovation and technology, a new and more efficient iron melting solution has emerged- Iron Melting Induction Furnaces.One company in particular (need remove brand name) has been making waves in this space, offering cutting-edge products that set a new standard for efficiency, reliability, and environmental sustainability. Their Iron Melting Induction Furnaces have been recognized by foundry operators as game-changing technology that vastly improves the melting process and reduces operating costs.The technology behind these furnaces is based on the principle of electromagnetic induction, where an alternating electric current generates magnetic fields that heat the metal in the crucible. Compared to traditional cupolas, iron melting induction furnaces have several advantages, including:• Faster Melting Time - Induction furnaces can melt iron in less than an hour, compared to several hours in a cupola furnace.• Cleaner Process - Induction melting does not use coke as fuel, eliminating the harmful emissions and pollution associated with cupolas.• Smaller Footprint - Induction furnaces require less floor space compared to cupolas, making them more suitable for small and medium-sized foundries.• Efficient Energy Use - Induction furnaces are highly energy-efficient, leading to significant cost savings and reduced carbon footprint.The (Need remove brand name) Iron Melting Induction Furnaces combine these benefits and go further by providing customizable solutions for specific foundry needs. Their furnace systems range from small portable models for hobbyists and small foundries to larger, fully automated solutions for high-volume production environments.Moreover, the company's furnaces are designed to be user-friendly, with easy-to-use digital interfaces that allow operators to monitor and control the melting process precisely. The company also provides training and after-sales service to ensure that their customers get the most value from their investment."The Iron Melting Induction Furnace is a revolutionary technology that is transforming the foundry industry," notes (Need remove brand name) company spokesperson. "Our goal has always been to provide cost-effective and environmentally sustainable solutions to our customers, and these furnaces accomplish both. By leveraging the power of electromagnetic induction, we've created a smarter and cleaner way to melt iron that saves time, space, and energy, without compromising on quality."As a result of these innovations, the iron melting induction furnace market is expected to grow rapidly in the coming years, as more foundries realize the benefits of this technology. According to a recent industry report, the iron melting induction furnace market is projected to reach $1.5 billion by 2026, growing at a CAGR of 6.5% from 2021 to 2026.In conclusion, the Iron Melting Induction Furnace is a transformative technology that is changing the face of the foundry industry. With its many advantages, including faster melting time, cleaner process, smaller footprint, and energy-efficient use, this technology is making iron melting more accessible and sustainable for foundries of all sizes. As (Need remove brand name) continues to lead the way in this space, we can expect to see more innovations that help foundries become more efficient, cost-effective, and environmentally sustainable.