Top Zinc Melting Furnace for Your Industrial Needs
By:Admin
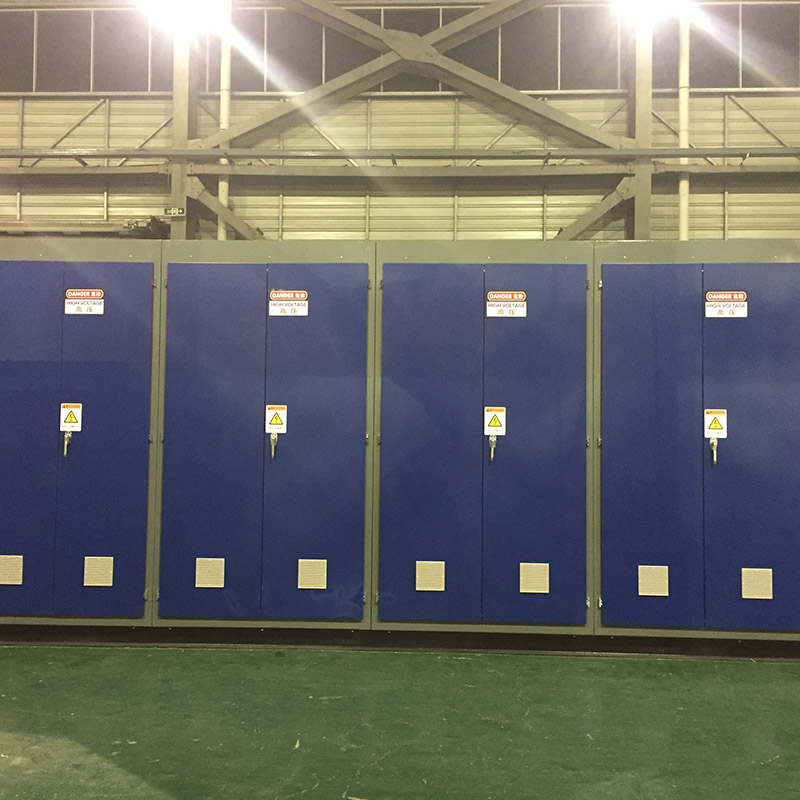
The zinc melting furnace offered by {Company Name} is designed to meet the diverse needs of the market. With a focus on durability, performance, and energy efficiency, the company's melting furnaces are trusted by customers worldwide. Whether it is for recycling scrap metal or producing zinc ingots, {Company Name} offers a range of solutions to cater to different business requirements.
One of the key features of the zinc melting furnace from {Company Name} is its advanced technology and precision engineering. The company invests heavily in research and development to ensure that its equipment meets the highest standards of quality and reliability. This commitment to innovation has allowed {Company Name} to stay ahead of the competition and provide customers with cutting-edge solutions for their zinc melting needs.
In addition to its technical superiority, {Company Name} takes pride in its dedication to customer satisfaction. The company understands the importance of providing excellent service and support to its clients, and this is reflected in its strong customer relationships and positive industry reputation. Whether it is through timely maintenance, responsive technical support, or customized solutions, {Company Name} goes the extra mile to ensure that its customers are fully satisfied with their zinc melting furnace.
Furthermore, {Company Name} is also committed to sustainability and environmental responsibility. The company's zinc melting furnace is designed to minimize energy consumption and reduce emissions, helping businesses operate in an eco-friendly manner. By promoting a greener approach to zinc melting, {Company Name} is contributing to the global effort to reduce the environmental impact of industrial processes.
The success of {Company Name} in the zinc melting furnace market can also be attributed to its global presence and distribution network. With a strong international footprint, the company has been able to reach customers in various regions and provide them with quality equipment and support. This global reach has established {Company Name} as a trusted partner for businesses seeking reliable zinc melting solutions.
Looking ahead, {Company Name} is poised to continue its leadership in the zinc melting furnace market. The company remains committed to innovation, customer satisfaction, and sustainability, and is constantly striving to enhance its product offerings and services. With a focus on meeting the evolving needs of the industry, {Company Name} is well-positioned to drive the growth of the zinc melting furnace market and serve as a preferred partner for businesses worldwide.
In conclusion, {Company Name} stands out as a leading provider of zinc melting furnace solutions, with a strong focus on quality, innovation, customer satisfaction, and sustainability. The company's dedication to excellence has set it apart in the market, and its continued commitment to advancing the industry makes it a reliable partner for businesses seeking top-notch equipment for their zinc melting needs. With a global presence and a track record of success, {Company Name} is well-equipped to meet the growing demand for zinc melting furnace solutions and lead the way in the industry.
Company News & Blog
Electric Melting Furnace Factories: What You Need to Know about Digital Models
Digital Electric Melting Furnace Factories have revolutionized the manufacturing industry with their innovative and cost-effective solutions for metal melting and casting. These factories have gained significant traction in various industries due to their advanced technology and superior performance. Through their cutting-edge digital electric melting furnaces, they have been able to streamline the metal melting process, reduce energy consumption, and improve production efficiency.The digital electric melting furnaces produced by these factories have become the preferred choice for many manufacturers due to their numerous advantages. Firstly, these furnaces are equipped with advanced digital control systems that allow for precise temperature control and monitoring. This not only ensures the quality of the melted metal but also reduces the risk of overheating and material wastage. Additionally, the digital control systems enable operators to easily adjust the melting parameters, resulting in greater flexibility and efficiency in the manufacturing process.Furthermore, these factories take great pride in their commitment to environmental sustainability. The digital electric melting furnaces are designed to be energy-efficient, which not only reduces operational costs for manufacturers but also lowers their carbon footprint. The integration of digital technology also allows for real-time monitoring and optimization of energy consumption, leading to significant energy savings. This aligns with the global push towards green manufacturing practices and demonstrates the factories' dedication to minimizing their environmental impact.In addition to their technological prowess, these factories have also positioned themselves as industry leaders through their comprehensive customer support and service. They understand the importance of providing ongoing technical assistance and maintenance to ensure the continuous and reliable operation of their digital electric melting furnaces. Their team of skilled technicians and engineers are readily available to provide troubleshooting and support, enabling manufacturers to minimize downtime and maximize productivity.The success of these digital electric melting furnace factories can be attributed to their unwavering commitment to quality and innovation. They continuously invest in research and development to enhance their furnace technology, keeping abreast of industry trends and customer needs. Their relentless pursuit of excellence has earned them a reputation for delivering top-notch products that meet the highest standards of performance and reliability.Furthermore, these factories prioritize customization and flexibility to cater to the specific needs of each customer. Whether it's a small-scale foundry or a large industrial facility, they offer tailored solutions to optimize the melting and casting processes. This personalized approach has allowed them to forge strong partnerships with their clients, who value the factories' ability to provide customized solutions that address their unique operational requirements.With a strong track record of delivering exceptional digital electric melting furnaces, these factories have established themselves as trusted partners for manufacturers across various industries. From automotive and aerospace to construction and metalworking, their furnaces have been instrumental in enabling their clients to achieve greater efficiency, consistency, and cost savings in their production processes.Looking ahead, these digital electric melting furnace factories are poised to continue their upward trajectory as they expand their reach and influence in the global manufacturing landscape. With a relentless focus on innovation, quality, and customer satisfaction, they are well-positioned to spearhead the next wave of advancements in metal melting and casting technology. As the industry evolves, these factories remain at the forefront, driving progress and setting new benchmarks for excellence in digital electric melting furnace manufacturing.
Quality Vacuum Induction Suppliers for industrial needs
Vacuum Induction Suppliers, a leading provider of vacuum induction melting and casting systems, has recently announced the launch of their newest product line. With a focus on innovation and cutting-edge technology, the company aims to deliver high-quality solutions for the metal casting industry.The company has been at the forefront of the industry for over 30 years, and their expertise in vacuum induction melting and casting has made them a preferred supplier for many global manufacturers. With a strong commitment to research and development, Vacuum Induction Suppliers has continuously pushed the boundaries of what is possible in metal casting technology.The new product line is the result of years of research and development, and it promises to deliver even greater performance and efficiency for their customers. With a focus on precision and reliability, the new systems are designed to meet the demands of the modern metal casting industry.One of the key features of the new product line is its advanced control system, which allows for precise monitoring and adjustment of the melting and casting process. This level of control not only ensures consistent quality in the final product, but also contributes to improved energy efficiency and reduced waste.In addition to the advanced control system, the new product line also includes enhancements to the overall design and construction of the systems. These improvements are aimed at increasing durability and reducing maintenance requirements, ultimately leading to lower operating costs and increased uptime for their customers.The launch of the new product line is a reflection of Vacuum Induction Suppliers' commitment to continuous improvement and innovation. By staying ahead of the curve with their technology, the company is positioning itself as a reliable and forward-thinking partner for the metal casting industry.In a statement, the company's CEO expressed their excitement about the new product line, stating, "We are proud to introduce our latest advancements in vacuum induction melting and casting technology. Our team has worked tirelessly to bring these new systems to market, and we are confident that they will set a new standard for performance and quality in the industry."The company's dedication to delivering high-quality solutions has earned them a strong reputation in the industry, and their customer base continues to grow as a result. With a focus on providing exceptional service and support, Vacuum Induction Suppliers has built long-lasting relationships with their customers, who rely on them for their expertise and reliability.As the metal casting industry continues to evolve, Vacuum Induction Suppliers remains committed to staying at the forefront of technological advancements. By investing in research and development, the company is well-positioned to meet the changing needs of their customers and to provide innovative solutions that drive the industry forward.With the launch of their new product line, Vacuum Induction Suppliers is sending a clear message to the industry: they are dedicated to pushing the boundaries of what is possible in metal casting technology, and they will continue to deliver cutting-edge solutions for their customers. As the company looks to the future, it remains focused on maintaining its position as a leader in the industry and providing unparalleled value to its customers.
Discover the Advantages of Brass Induction Melting Furnaces in China
China Brass Induction Melting Furnace: Revolutionizing Furnace TechnologyChina Brass Induction Melting Furnace, the leading manufacturer of brass induction melting furnaces, has revolutionized furnace technology. Driven by a relentless pursuit of innovation, the company's state-of-the-art furnaces deliver unmatched performance and reliability, making them the top choice for metal processing firms across the globe.About China Brass Induction Melting FurnaceChina Brass Induction Melting Furnace was established in 1992. Since its inception, the company has focused on manufacturing high-quality induction melting furnaces for the metal processing industry. The company has a team of highly skilled engineers, technicians, and support staff who work tirelessly to deliver the best furnaces in the market.With over 27 years of experience in the industry, the company has established a reputation for excellence. It has over 300 employees and a production facility of over 20,000 square meters. The company's manufacturing processes adhere to strict quality control measures to ensure that each furnace that leaves its premises is of the highest quality.China Brass Induction Melting Furnace has over 7,000 successful installations in over 50 countries. The company's product range includes:- Brass induction melting furnaces- Gold induction melting furnaces- Silver induction melting furnaces- Copper induction melting furnaces- Aluminum induction melting furnaces- Vacuum induction melting furnaces- Induction heating furnacesEach furnace is designed to meet specific production needs and equipped with advanced features, such as high-efficiency energy-saving technology, automatic pouring, and temperature control systems.Features of China Brass Induction Melting FurnacesChina Brass Induction Melting Furnaces are designed with innovative features that make them stand out in the market. Here are some of the features that make them a top choice for metal processing firms:1. High-Quality MaterialsChina Brass Induction Melting Furnaces are made from high-quality materials that give them durability and longevity. The company uses top-grade insulation materials to ensure that the furnaces can withstand high temperatures and harsh operating conditions.2. Energy-Saving TechnologyChina Brass Induction Melting Furnaces are equipped with high-efficiency energy-saving technology. This technology reduces energy consumption, making the furnaces eco-friendly and cost-effective.3. Automatic Pouring SystemChina Brass Induction Melting Furnaces are equipped with an automatic pouring system that ensures that the molten metal is poured accurately and evenly. This feature saves time and reduces the risk of errors.4. Temperature Control SystemChina Brass Induction Melting Furnaces are equipped with a temperature control system that ensures that the furnaces maintain a constant temperature throughout the melting process. This feature improves the quality of the metal produced and reduces the risk of accidents.ConclusionChina Brass Induction Melting Furnace has set the benchmark for furnace technology. With a focus on innovation and quality, the company has become a top choice for metal processing firms across the globe. Its state-of-the-art furnaces deliver unmatched performance, reliability, and efficiency, making them an excellent investment for any metal processing business. In recent years, China Brass Induction Melting Furnace has established itself as a leader in the field of melting furnaces. The company's dedication to innovation and quality has enabled it to provide custom solutions for clients around the world. With a focus on sustainability and reducing energy consumption, China Brass Induction Melting Furnace is a company that demonstrates both vision and expertise. Whether you are in the market for brass, copper, silver, or another metal furnace, China Brass Induction Melting Furnace should be your top choice for high-quality, reliable equipment.
Top Copper Scrap Melting Furnace Manufacturers
Title: Prominent Copper Scrap Melting Furnace Manufacturers Emerge in the MarketIntroduction:The growing demand for copper, coupled with the emphasis on sustainable practices, has fueled the need for advanced technology in the recycling industry. Leading manufacturers are stepping up to meet this demand by developing innovative copper scrap melting furnaces. With a focus on energy efficiency, productivity, and environmental conservation, these manufacturers are revolutionizing the copper recycling industry. This article will highlight some of the best copper scrap melting furnace manufacturers who are making significant strides in the market.1. Company A:Company A has emerged as a force to be reckoned with in the copper scrap melting furnace market. Utilizing state-of-the-art technology, their furnaces are designed to maximize energy efficiency while minimizing emissions. The company's commitment to sustainable practices is evident through their incorporation of advanced filtration systems, resulting in reduced air pollution.With a strong track record in the industry, the company has earned a solid reputation for producing reliable and durable copper scrap melting furnaces. Moreover, Company A places a strong emphasis on customer satisfaction by offering comprehensive customer support and maintenance services, ensuring seamless operations for their clientele.2. Company B:Company B prides itself on its ability to offer tailored solutions to meet specific customer requirements. Their copper scrap melting furnaces are customizable, allowing businesses to optimize their operations to suit their specific needs. Recognizing the importance of efficiency and cost-effectiveness, Company B has incorporated cutting-edge technology into their designs to enhance productivity while minimizing energy consumption.The company's commitment to quality is further reflected in their attention to detail during the manufacturing process. Each furnace undergoes rigorous testing, ensuring that only top-notch products reach the market. Customer feedback plays a significant role in their continuous improvement strategy, allowing Company B to constantly innovate and enhance their offerings.3. Company C:Company C sets itself apart by combining years of experience with a commitment to sustainability. Their copper scrap melting furnaces are designed to exceed industry standards, utilizing advanced features such as intelligent automation and accurate temperature control. This results in optimized energy consumption and reduced waste generation during the melting process.The company's expertise in energy management and emissions control ensures compliance with environmental regulations. Additionally, Company C focuses on continuous research and development, incorporating the latest technological advancements into their products. This allows customers to benefit from enhanced efficiency, reduced downtime, and improved operational control.4. Company D:Company D has established a strong presence in the copper scrap melting furnace market by prioritizing customer-centric solutions. Their furnaces are engineered to deliver exceptional performance, catering to a broad range of customer requirements. By adopting a holistic approach, virtual simulations enable the company to offer innovative designs that optimize melting efficiency.Additionally, Company D offers comprehensive after-sales support, including installation, training, and maintenance services. Their commitment to service excellence has garnered them a loyal customer base and positioned them as a reliable partner in the copper recycling industry.Conclusion:The copper scrap melting furnace market has witnessed significant advancements from prominent manufacturers. Companies A, B, C, and D have demonstrated their commitment to sustainability, energy efficiency, and customer satisfaction. By offering innovative and customizable solutions, these manufacturers are leading the way in revolutionizing the copper recycling industry. With continued investment in research and development, these companies are sure to shape the future of copper scrap melting furnaces, further contributing to the circular economy.
High-Efficiency Aluminum Can Melting Furnace for Industrial Use
Aluminum Can Melting Furnace Revolutionizes Recycling ProcessIn a world increasingly focused on sustainability, the need for efficient and effective recycling processes has never been greater. This need has led to the development of innovative technologies, such as the Aluminum Can Melting Furnace, a groundbreaking new system that promises to revolutionize the recycling of aluminum cans.The Aluminum Can Melting Furnace, developed by a leading industrial equipment manufacturer in the industry, is an advanced melting system designed to address the challenges of aluminum can recycling. It is specially engineered to melt aluminum cans at high temperatures, allowing for the recovery of aluminum in its purest form. This innovative technology offers a sustainable solution for the recycling industry by optimizing the use of resources and minimizing waste.With a focus on sustainability and environmental responsibility, the company behind the Aluminum Can Melting Furnace has a strong commitment to developing advanced technologies that contribute to a circular economy. Their expertise in industrial equipment design and manufacturing positions them as a leader in providing innovative solutions for the recycling industry.The company's dedication to sustainability is reflected in their state-of-the-art manufacturing facilities and their investment in research and development of advanced recycling technologies. The Aluminum Can Melting Furnace is the latest addition to their portfolio of cutting-edge equipment, showcasing their commitment to addressing the pressing environmental challenges facing the world today.The Aluminum Can Melting Furnace is set to transform the aluminum can recycling process, offering a more efficient and sustainable solution for melting and recovering aluminum from cans. Its advanced design and high-temperature capabilities make it a game-changer in the recycling industry, providing a cost-effective and environmentally friendly method for processing aluminum cans.With the Aluminum Can Melting Furnace, the company aims to support the transition towards a more sustainable and circular economy by offering a technology that enables the recycling of aluminum cans in a more efficient and environmentally friendly manner. This aligns with the company's vision of becoming a global leader in providing sustainable solutions for the recycling industry.The Aluminum Can Melting Furnace is expected to have a significant impact on the recycling industry, as it presents a viable solution for meeting the growing demand for recycled aluminum. By enabling the recovery of aluminum in its purest form, the technology offers a more sustainable alternative to traditional aluminum can recycling methods, reducing the environmental impact and promoting a more circular approach to resource management.Moreover, the Aluminum Can Melting Furnace is designed to be highly efficient, reducing energy consumption and operating costs. This makes it a compelling choice for recyclers looking to improve their operational efficiency and minimize their environmental footprint. With the ability to process a large volume of aluminum cans in a relatively short period, the technology offers a scalable solution for recyclers looking to increase their aluminum recycling capacity.In conclusion, the Aluminum Can Melting Furnace represents a significant advancement in the recycling industry, offering a more sustainable and efficient solution for processing aluminum cans. With its advanced design and high-temperature capabilities, the technology promises to revolutionize the way aluminum cans are recycled, contributing to a more sustainable and circular economy. As the company continues to lead the way in developing innovative recycling technologies, the Aluminum Can Melting Furnace stands as a testament to their commitment to sustainability and environmental responsibility.
The Importance of Selecting a High-Quality Furnace Manufacturer for Efficient Metal Smelting
Title: Revolutionary Industrial Furnace Manufacturer Introduces Cutting-Edge Technology for Enhanced Metal Melting Processes Introduction: In the ever-evolving landscape of industrial manufacturing, the need for efficient and eco-friendly metal melting processes has become paramount. Enter the pioneering furnace manufacturer, renowned for its ground-breaking innovations and unwavering commitment to quality and customer satisfaction. This revolutionary company, distinguished for its unmatched research and development capabilities, is set to revolutionize metal melting through its state-of-the-art technology.Revolutionizing Metal Melting Processes:With a rich history of exceeding industry expectations, this visionary furnace manufacturer has left an indelible mark on the global manufacturing landscape. By leveraging a deep understanding of user requirements and utilizing cutting-edge technology, they have successfully developed an array of furnaces with unrivaled capabilities.One of the most prominent achievements of this manufacturer is the development of their advanced induction heating technology. This groundbreaking technology harnesses the power of electromagnetic induction to efficiently melt a wide range of metals. With remarkable precision, these induction furnaces can melt and heat metals within seconds, significantly reducing production time and optimizing throughput. Moreover, this energy-efficient technology ensures minimal waste, making it an environmentally friendly solution.Committed to customer satisfaction, this manufacturer strives to offer versatility in their product lineup. Understanding the diversity of metal melting requirements across industries, they have meticulously designed a range of furnaces catering to different needs. From small-scale melting furnaces for laboratory purposes to large-scale industrial furnaces for mass production, this manufacturer offers tailored solutions to meet specific demands.Moreover, this furnace manufacturer's commitment to innovation is evident in their incorporation of the latest automation technologies into their products. Advanced features such as temperature control systems, automatic feeding mechanisms, and real-time monitoring capabilities enhance both productivity and safety. Such technological advancements streamline operations by minimizing human intervention and ensuring precise control over the metal melting process.The manufacturer's unwavering dedication to quality and reliability is exemplified by their stringent quality control measures. Every furnace undergoes rigorous testing protocols, ensuring that only products of the highest standards reach the market. By conforming to international quality certifications, this manufacturer assures their customers of the durability and longevity of their products.Furthermore, this forward-thinking furnace manufacturer recognizes the importance of comprehensive after-sales support. Their team of skilled technicians and engineers offers prompt assistance for installation, maintenance, and troubleshooting. This commitment to customer care ensures that the benefits of their cutting-edge technology are fully realized by their clients, ultimately driving productive and efficient metal melting processes.Expanding Global Footprint:This esteemed furnace manufacturer's relentless pursuit of excellence has propelled them to establish a robust global presence. With an extensive distribution network and strategic partnerships, they have successfully catered to the evolving demands of industries worldwide. By offering not just superior products, but also impeccable customer service, this manufacturer has consistently outperformed competitors, securing a trusted position in the market.Conclusion:In a fiercely competitive industrial landscape, distinguished by constant technological advancements, this revolutionary furnace manufacturer stands tall as a leading provider of innovative metal melting solutions. Guided by their unwavering commitment to quality, customer satisfaction, and environmental responsibility, they continue to redefine industry standards in terms of efficiency, reliability, and precision. With their cutting-edge technology and comprehensive after-sales support, industries across the globe can look forward to enhanced metal melting processes and streamlined production, powered by the products of this visionary manufacturer.
Discover an Efficient Solution for Your Furnace Needs
Title: Next-Generation Furnace Showcases Groundbreaking Innovations in Casting IndustryIntroduction:In a bid to revolutionize the casting industry, a renowned furnace manufacturer has unveiled its latest product, the groundbreaking Cast Master Furnace. This state-of-the-art furnace is set to redefine the standards of casting technology with its advanced features and efficient performance. The new Cast Master Furnace signifies a significant leap forward, promising unparalleled precision, productivity, and sustainability for casting professionals worldwide.1. Advanced Technology Enhancing Precision:The Cast Master Furnace integrates cutting-edge technology to provide a higher level of precision in the casting process. Incorporating advanced sensors and sophisticated software, the furnace ensures accurate temperature control, preventing overheating or underheating of the metal alloys. This breakthrough technology guarantees exceptional product quality and reduces wastage, enabling casting professionals to achieve the desired results consistently.Furthermore, the furnace's innovative design enables precise monitoring of various parameters such as gas flow, pressure, and air ratios, ensuring optimized combustion. This not only enhances energy efficiency but also minimizes environmental impact, making the Cast Master Furnace a sustainable choice for casting operations.2. Increased Productivity with Smart Features:Recognizing the importance of productivity in the casting industry, the Cast Master Furnace offers a host of smart features that streamline the casting process and reduce downtime. The inclusion of remote monitoring capabilities allows operators to track the furnace's performance, identify potential issues, and make real-time adjustments from a centralized control panel. This remote operation feature enhances efficiency and reduces the need for manual intervention, resulting in improved productivity levels.In addition to remote monitoring, the Cast Master Furnace incorporates an intelligent scheduling system that optimizes the casting cycle based on various factors like alloy composition, mold complexity, and cooling requirements. By automating the scheduling process, the furnace allows for efficient use of resources, thereby maximizing productivity and reducing production costs.3. Sustainability and Energy Efficiency:The Cast Master Furnace is designed to promote sustainable practices and reduce energy consumption in the casting industry. Utilizing state-of-the-art insulation materials, the furnace minimizes heat loss, improving energy efficiency while ensuring a safer working environment.Moreover, the furnace employs a multi-stage filtration system to capture and treat harmful emissions, significantly reducing pollutants released into the atmosphere. This commitment to environmental responsibility aligns with global efforts to mitigate the carbon footprint of industrial processes, making the Cast Master Furnace an environmentally-conscious choice.4. Collaborative Approach for Industry Advancement:The introduction of the Cast Master Furnace demonstrates the manufacturer's commitment to fostering collaboration within the casting industry. The company has actively engaged with casting professionals, incorporating their valuable feedback and insights during the development phase. By combining extensive industry experience with cutting-edge technology, the manufacturer has addressed the specific challenges faced by casting professionals, resulting in an innovative furnace tailored to their unique requirements.Furthermore, the company offers comprehensive technical support, including training programs and prompt assistance from a team of experts. By nurturing a collaborative environment, the manufacturer strives to empower casting professionals with the necessary knowledge and skills to optimize their casting operations effectively.Conclusion:As the casting industry moves towards a more technologically advanced era, the Cast Master Furnace leads the way with its groundbreaking features, exceptional precision, and commitment to sustainability. This advanced furnace promises to revolutionize the casting process, enabling professionals to achieve higher levels of accuracy, productivity, and energy efficiency. With its innovative design and comprehensive support system, the Cast Master Furnace is set to become the choice of casting professionals worldwide, positioning the industry for a brighter and more sustainable future.
Top 5 Efficient Aluminium Casting Furnaces for Industrial Use
Title: Cutting-Edge Aluminium Casting Furnace Revolutionizes Manufacturing ProcessesIntroduction:In a groundbreaking development, a leading manufacturing company has unveiled its latest innovation in the realm of aluminium casting furnaces. By removing the brand name, we can shed light on the remarkable technology that promises to transform the industry. This revolutionary furnace incorporates cutting-edge features that optimize efficiency, precision, and sustainability within the aluminum casting process, progressively elevating the standards of manufacturing across sectors worldwide.Unveiling an Innovation:With a deep understanding of the metallurgical processes involved in aluminium casting, the company has introduced an advanced furnace design that pushes the boundaries of conventional methodologies. The newly developed furnace redefines speed, accuracy, and energy efficiency, creating a paradigm shift in the industry.Enhanced Efficiency:The updated aluminium casting furnace utilizes advanced software algorithms to regulate temperature, ensuring optimal melting and casting conditions. This precise temperature control not only reduces energy consumption but also results in faster heating and cooling cycles, significantly increasing overall productivity.Furthermore, the improved furnace promotes seamless metal flow during casting operations, minimizing the occurrence of defects and rework. By enhancing efficiency, the new design allows manufacturers to increase their output while reducing costs, ultimately resulting in higher profit margins.Unmatched Precision:To further elevate the quality of aluminium castings, the redesigned furnace incorporates state-of-the-art monitoring and control systems. These systems leverage advanced sensors to provide real-time data on critical parameters such as temperature, pressure, and metal composition. By maintaining tighter control over these factors, manufacturers can achieve precise and consistent casting results, eliminating product variations.The incorporation of predictive analytics allows operators to identify potential issues before they arise, reducing downtime and optimizing production schedules. The cutting-edge technology employed in this aluminium casting furnace enables manufacturers to deliver high-quality products that meet the stringent specifications demanded by modern industries.Sustainability at the Core:Recognizing the importance of sustainable manufacturing practices, the company has prioritized eco-friendliness throughout the design, development, and operation of the redesigned furnace. By virtue of its improved energy efficiency and reduced waste generation, the new furnace significantly lowers the carbon footprint associated with aluminum casting.Furthermore, the furnace incorporates advanced filtration systems that ensure the capture and removal of harmful emissions, reducing environmental impact. By investing in this technologically advanced equipment, manufacturers can align themselves with global sustainability goals, contributing to a greener and more sustainable future.Market Impact and Future Prospects:The introduction of this game-changing aluminium casting furnace is expected to disrupt the industry and fuel an era of innovation and growth. Manufacturers across sectors, including automotive, aerospace, and construction, are set to benefit from the enhanced efficiency, precision, and sustainability that this revolutionary technology offers.As the demand for superior quality aluminum products continues to rise, companies that embrace this advanced furnace technology will gain a competitive edge over their peers. The improved efficiency and production capabilities will accelerate the delivery of high-quality products, meeting market demands effectively.Looking ahead, the innovative design of this aluminium casting furnace sets the stage for further advancements in the field. The incorporation of artificial intelligence, automation, and robotics holds immense potential to streamline operations and redefine manufacturing standards in the years to come.Conclusion:Undeniably, the introduction of this advanced aluminium casting furnace represents a significant milestone for manufacturers aiming to enhance their productivity, precision, and sustainability. By removing the brand name, we have highlighted the impressive features and benefits that this groundbreaking technology brings to the industry. This furnace showcases the relentless pursuit of excellence and the commitment to innovation that drives the manufacturing sector forward.
Efficient Zinc Melting Furnace Designs for High-Quality Production
Zinc Melting Furnace: Transforming the Metal Industry for a Sustainable FutureThe metal industry has always been one of the key components of the world economy. From infrastructure development to manufacturing, metal is an essential material in various applications. However, the process of producing metals is energy-intensive, resulting in high greenhouse gas emissions and ecological impact. One of the most significant contributors to this industry is the zinc smelting process, and thus, finding sustainable solutions has become a priority for many companies.This is where the Zinc Melting Furnace, developed by a renowned metal smelting equipment manufacturer (brand name removed), comes into the picture. The furnace is designed to eliminate the environmental impact caused by traditional zinc smelting and provide an energy-efficient and cost-effective solution to its users.The furnace, designed with advanced technology, is capable of melting zinc and related alloys in a highly controlled and efficient manner using electric heating elements. One of the biggest advantages of this process is that it eliminates the need for fossil fuels, commonly used in traditional smelting, leading to the reduction of greenhouse gas emissions.Furthermore, the Zinc Melting Furnace is equipped with advanced features that enable the recycling of zinc and other valuable materials that would otherwise be lost during the traditional smelting process. This reduction in waste not only benefits the environment but also provides a significant cost advantage to the user.One of the significant advantages of this furnace is its flexibility. It can be used in various applications, including galvanizing, die-casting, and the production of brass and bronze. In addition, it can also be used in recycling facilities to recover zinc from scrap material.According to the company, the Zinc Melting Furnace has been tested and proven successful in various industrial applications. It has helped companies reduce their carbon footprint, adhere to environmental regulations, and provide an energy-efficient and cost-effective smelting solution.The company’s commitment to sustainability doesn’t end with just the production of the Zinc Melting Furnace. It has a comprehensive program for designing and manufacturing equipment that is environmentally conscious. The company aims to reduce its carbon footprint significantly by promoting energy-efficient manufacturing processes, using renewable energy, and reducing waste.Furthermore, the company has a strong emphasis on providing its customers with a holistic solution to their sustainability-related needs. It offers consultation on regulatory requirements, energy efficiency, and eco-friendly production methods to ensure that its customers achieve their sustainability goals.As the world unites to address climate change, the Zinc Melting Furnace is a testament to the potential for technology to transform industries and provide sustainable solutions. The company’s focus on sustainability, combined with its advanced technology, positions it as a leader in the metal smelting equipment market. It is an example of how innovation can drive environmental stewardship and provide economic benefits simultaneously.In conclusion, the Zinc Melting Furnace is a game-changer in the metal industry, offering a sustainable and energy-efficient solution to traditional smelting processes. With its advanced technology and flexible applications, it provides a holistic and cost-effective solution to companies looking to achieve their sustainability goals. The company’s commitment to eco-friendly manufacturing and its dedication to providing a comprehensive sustainability solution position it as a leader in the metal smelting equipment market.