- Home
- News
- Cutting-Edge Vacuum Casting Furnace Technology Unveiled for Enhanced Manufacturing Processes
Cutting-Edge Vacuum Casting Furnace Technology Unveiled for Enhanced Manufacturing Processes
By:Admin
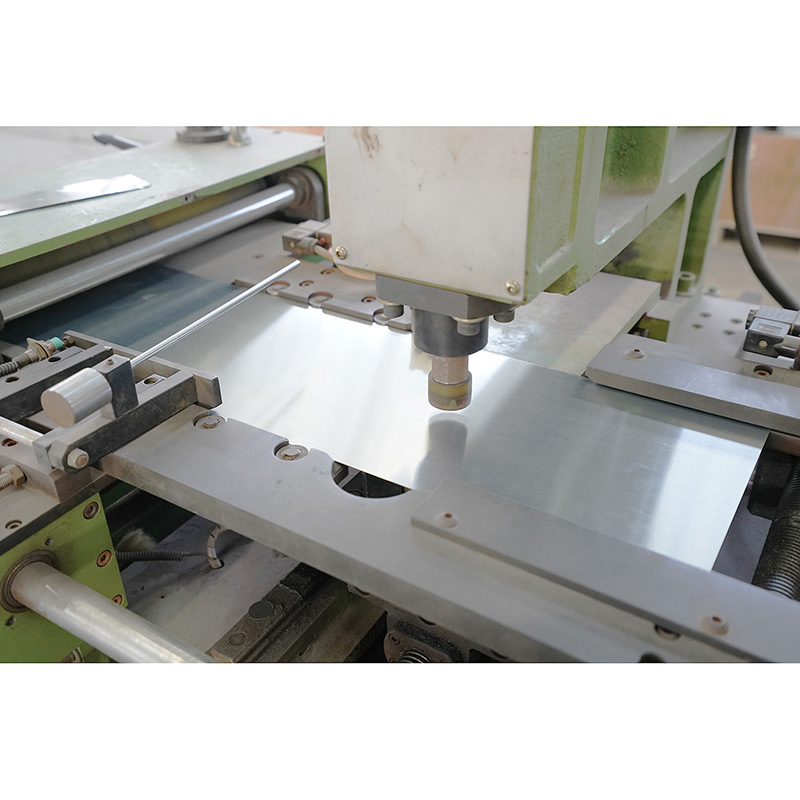
Company News & Blog
Top Metal Induction Furnace Factory in the News
Title: Innovative Metal Induction Furnace Factory Sets New Industry StandardsIntroduction:In a fast-paced world driven by technological advancements, industries are constantly seeking innovative solutions to improve efficiency and productivity. The Best Metal Induction Furnace Factory, a leading player in the metal industry, has become renowned for revolutionizing the metal induction furnace manufacturing process. With a commitment to excellence and a customer-centric approach, this factory has redefined industry standards, empowering businesses with cutting-edge technology and sustainable solutions.I. Pioneering Research and Development Initiatives:With an unwavering focus on technological advancement, the Best Metal Induction Furnace Factory has established itself as a trailblazer in the industry. Invested in research and development, the factory consistently works towards creating breakthrough technologies, ensuring customers receive the most efficient, cost-effective, and reliable induction furnaces available in the market.II. State-of-the-Art Manufacturing Facilities:The Best Metal Induction Furnace Factory boasts state-of-the-art manufacturing facilities equipped with advanced machinery and tools. This enables the factory to deliver high-quality, precision-engineered furnaces that meet the diverse needs of its clientele. The factory's commitment to excellence extends throughout the manufacturing process, ensuring each furnace adheres to the strictest quality standards.III. Sustainability and Energy Efficiency:The Best Metal Induction Furnace Factory recognizes the importance of sustainability and endeavors to minimize its environmental impact. By incorporating energy-efficient features in their furnace designs, the factory aids businesses in reducing their carbon footprint and operating costs. The induction furnaces are designed to optimize energy consumption, making them an ideal choice for environmentally conscious industries.IV. Customization Options:Understanding that every business has unique requirements, the factory offers a wide range of customizations to accommodate diverse needs. With a team of skilled professionals, the factory collaborates closely with customers to understand their specific demands and provides tailored solutions. This flexibility ensures seamless integration of the induction furnaces into existing production lines while maximizing productivity and efficiency.V. Exceptional After-Sales Support:The Best Metal Induction Furnace Factory not only focuses on delivering exceptional products but also prioritizes providing unparalleled after-sales support. Recognizing the importance of minimizing downtime, the factory offers prompt technical assistance, maintenance services, and spare parts availability to ensure uninterrupted operations. This commitment to customer satisfaction has garnered the factory a loyal customer base.VI. Industry Recognition and Awards:The Best Metal Induction Furnace Factory's dedication to excellence and innovation has garnered recognition from various industry bodies. The factory takes great pride in accolades received for its contributions to the industry, including awards for technological breakthroughs, product quality, and sustainability efforts. These achievements reflect the factory's commitment to pushing boundaries and setting new standards.VII. Global Presence and Expansion:Driven by its success and industry reputation, the Best Metal Induction Furnace Factory has expanded its operations worldwide. With a global presence, the factory has established partnerships with businesses, both small and large, seeking cutting-edge induction furnace technology. This expansion further solidifies the factory's position as a global leader and reaffirms its commitment to serving industries across the globe.Conclusion:The Best Metal Induction Furnace Factory's relentless pursuit of innovation, impeccable manufacturing capabilities, focus on sustainability, and commitment to customer satisfaction have set it apart in the industry. By redefining industry standards and providing businesses with state-of-the-art metal induction furnaces, the factory continues to empower industries, enhance productivity, and shape the future of the metal industry on a global scale.
Top Manufacturer for Induction Furnace Cooling Systems Revealed
piece:Induction Furnace Cooling System: The Secret Behind Efficient Metal MeltingInduction furnaces are among the most innovative and effective ways of melting metals, and they operate by using electromagnetic induction to heat up and melt metals. Unlike traditional furnaces that rely on heating elements, induction furnaces produce heat through electromagnetic currents, making them more efficient, faster, and safer than their conventional counterparts.However, as with most advanced technologies, they come with a few maintenance challenges. One of the most significant challenges is maintaining the ideal operating temperature through the efficient cooling of the system. If an induction furnace's temperature exceeds the recommended levels, it can cause severe damage to the furnace, resulting in costly repairs or even machine replacement.To prevent this from happening, induction furnace manufacturers need to integrate the best cooling systems, preferably those from a reliable cooling system manufacturer, to ensure optimal furnace performance.For those in search of the best induction furnace cooling system manufacturer, look no further than the leading cooling system company. The company is a global player in the cooling system industry, with a reputation for designing and manufacturing innovative and high-quality cooling systems for various industrial applications.The company's induction furnace cooling systems are designed to provide a reliable, stable, efficient, and cost-effective cooling solution for all types of furnaces, including induction furnaces. They provide the necessary cooling capacity, whether for continuous or intermittent operations, ensuring prolonged furnace life, enhanced performance, and increased productivity.One of the most significant advantages of the company's induction furnace cooling systems is their energy efficiency. The cooling systems are designed to operate with lower power consumption while still maintaining optimal cooling capacity. This translates to lower energy bills and reduced carbon footprint, which is excellent news for environmentally conscious furnace operators.In addition to their energy efficiency, the cooling systems are designed for ease of installation and maintenance, thanks to the modular design and user-friendly interface. The company's commitment to excellent customer service means that they provide comprehensive pre and post-installation support to customers, including on-site installation and training, and remote troubleshooting and maintenance services.The company's induction furnace cooling systems have proven reliability, having been subjected to rigorous testing and inspection before release to the market. They are made from the highest quality materials and components, ensuring durability, functionality, and performance consistency.The company's cooling systems feature cutting-edge technologies, such as intelligent temperature control, real-time monitoring, and automatic adjustment of cooling capacity. These technologies prevent overheating, drastic temperature changes, and other furnace malfunctions that could cause damage to the equipment or the melted metals.In conclusion, induction furnaces are an excellent option for industrial metal melting applications, and the cooling system is a crucial component to ensure optimal furnace performance. While several induction furnace cooling system manufacturers are available in the market, the leading cooling system company stands out from the crowd for their energy efficiency, reliability, durability, and functionality. Their induction furnace cooling systems provide a reliable and efficient cooling solution for all furnace types while ensuring extended furnace life, productivity, and enhanced performance. Contact the company today for a bespoke induction furnace cooling system to suit your furnace's unique needs.
Discover the Latest Innovation in High-Quality Smelting Equipment
Title: Advanced Smelting Equipment Revolutionizes Company OperationsIntroduction:In a significant milestone for the manufacturing industry, a leading company in the field of smelting equipment has developed state-of-the-art machinery that is set to revolutionize the way companies carry out their smelting processes. Fueled by years of research and development, this cutting-edge equipment promises to enhance efficiency, productivity, and sustainability, presenting a new era for companies engaged in metal refining and other related activities. With an unwavering dedication to innovation, this company is making strides to reshape the industry landscape, offering businesses a competitive edge in the global market.I. Smelting Equipment's Technological Breakthrough:The newly developed smelting equipment, (remove brand name), represents a technological breakthrough for the industry. It incorporates advanced features and functionalities that streamline the smelting process, offering significant advantages to companies looking to optimize their operations. With an emphasis on efficiency and sustainability, this cutting-edge equipment is built to minimize energy consumption, reduce waste, and enhance the overall quality of the end product.The equipment's intelligent monitoring system ensures accurate temperature control, resulting in improved metal purity and reduced material losses. Additionally, the incorporation of automation technology not only minimizes the risk of human error but also enables the equipment to operate continuously for extended periods, significantly boosting production capacity.II. Enhanced Safety Measures:In line with industry demands for improved safety standards, the smelting equipment integrates comprehensive safety measures to protect both operators and the environment. The introduction of advanced sensors and alarms monitors critical parameters such as temperature, pressure, and gas concentration, promptly alerting operators to any potential risks or deviations. This proactive approach ensures a safer working environment and minimizes the likelihood of accidents.Furthermore, the equipment is designed with a state-of-the-art waste gas treatment system, effectively reducing emissions and adhering to stringent environmental regulations. By minimizing environmental impact, companies utilizing this advanced smelting equipment demonstrate their commitment towards sustainable manufacturing practices.III. Improved Cost-efficiency and Resource Optimization:With the new smelting equipment, companies can expect significant cost savings and resource optimization. The integration of precision control mechanisms maximizes the extraction of valuable metals from raw materials, reducing the amount of waste generated. This enhanced efficiency not only reduces material costs but also contributes to a more sustainable use of available resources.Moreover, the equipment's intelligent energy management system optimizes power consumption by regulating energy output during peak and low demand periods. This results in reduced energy bills for companies and a smaller overall carbon footprint, aligning with contemporary goals of environmental stewardship.IV. Market Competitiveness and Global Reach:With the adoption of this advanced smelting equipment, companies gain a competitive edge in the global market. The increased efficiency and improved product quality achieved through the equipment's cutting-edge technology allow businesses to meet customer demands more effectively and respond to market fluctuations with greater agility.By embracing sustainability and incorporating state-of-the-art equipment into their manufacturing processes, companies utilizing this smelting equipment can market their products as environmentally responsible and gain a competitive advantage in increasingly eco-conscious markets.V. Company's Commitment to Innovation:The development and launch of this breakthrough smelting equipment signify the company's commitment to ongoing innovation and industry leadership. With a dedicated research and development team, the company continues to leverage the latest technology to enhance its offerings, meeting the evolving needs of the industrial sector.As a leading provider of smelting equipment, the company remains focused on providing comprehensive solutions to its customers and contributing to the advancement of the manufacturing industry as a whole. Their dedication to innovation ensures that businesses can achieve improved operational efficiencies, environmental sustainability, and increased profitability.Conclusion:The unveiling of advanced smelting equipment by (remove brand name) marks a revolutionary turning point for manufacturing companies engaged in metal refining. With enhanced efficiency, safety, and sustainability, this cutting-edge equipment empowers businesses to optimize their smelting processes, reduce costs, and gain a competitive edge in the global market. As the company continues to spearhead innovation, the future of the smelting industry looks increasingly promising, ushering in a new era of heightened performance and environmental responsibility.
Discover the Efficiency and Versatility of Copper Melting Kilns
Title: Advanced Kiln Revolutionizes Copper Melting ProcessIntroduction:In a breakthrough development for the metal industry, a pioneering company has launched a state-of-the-art kiln designed specifically for the efficient and sustainable melting of copper. This new kiln, developed by a leading manufacturer in collaboration with industry experts, promises to revolutionize the copper melting process by combining cutting-edge technology with eco-friendly features.Paragraph 1:Copper, known for its versatility and conductivity, is a vital component in various industries, including electronics, construction, and transportation. However, the traditional methods of melting copper have often been associated with energy inefficiency and harmful emissions. Recognizing the need for a more sustainable solution, innovative manufacturer [Company Name] has introduced a groundbreaking kiln that addresses these challenges head-on.Paragraph 2:The new kiln, which combines advanced engineering with eco-friendly features, aims to maximize energy efficiency, reduce greenhouse gas emissions, and optimize the copper melting process. By using state-of-the-art technology, [Company Name] has developed a highly-effective system that ensures minimal energy loss throughout the melting cycle, resulting in reduced operational costs and a significantly smaller carbon footprint.Paragraph 3:Moreover, the kiln's intelligent heating system allows for precise temperature control, facilitating the melting of copper at optimal conditions. This cutting-edge technology not only enhances the quality of the final product but also minimizes waste and decreases the need for rework, thereby boosting overall productivity and competitiveness.Paragraph 4:The kiln's design is also focused on the safety and well-being of operators. With advanced safety features such as automatic shut-off mechanisms and real-time monitoring systems, [Company Name] prioritizes the protection and welfare of its workers, minimizing risks and accidents in the workplace.Paragraph 5:To manufacture this groundbreaking equipment, [Company Name] has partnered with leading experts in the field of copper melting and metal processing. By leveraging their extensive knowledge and expertise, [Company Name] has ensured that their kiln is not only technologically advanced but also meets the specific requirements and challenges faced by the copper industry.Paragraph 6:Recognizing the importance of sustainability, [Company Name] has integrated eco-friendly practices throughout the kiln's lifecycle. By using recycled and durable materials during production, implementing energy-saving components, and prioritizing recyclability during disposal, the company aims to minimize environmental impact while consistently delivering high-performance, cost-effective kilns to their clients.Paragraph 7:The launch of this groundbreaking kiln is expected to significantly impact the copper industry, offering a greener and more efficient alternative to traditional copper melting methods. As the demand for sustainable practices continues to grow, [Company Name] is at the forefront of driving innovation, helping countless businesses reduce their environmental footprint while maximizing productivity.Conclusion:With the launch of their advanced kiln for melting copper, [Company Name] has demonstrated their commitment to pushing the boundaries of engineering excellence and sustainability. This revolutionary equipment promises to transform the way copper is melted, minimizing energy consumption, reducing emissions, and ensuring a safer and more productive manufacturing process. As the industry looks towards a greener future, [Company Name] is leading the way with their cutting-edge kiln technology.
Top Aluminum Smelting Equipment for Efficient and Sustainable Production
Aluminum Smelting Equipment Company Unveils New State-of-the-Art Metal Smelting ProcessAluminum Smelting Equipment Company, a leading provider of aluminum smelting equipment and services, has recently introduced a new state-of-the-art metal smelting process that promises to revolutionize the industry.The company has long been committed to providing its customers with innovative and cost-effective solutions for aluminum smelting. Its new smelting process builds on years of experience and expertise in the field, incorporating the latest technological advancements to deliver unparalleled efficiency and quality in the production of aluminum.The new process utilizes a combination of advanced smelting techniques and cutting-edge equipment to produce aluminum in a highly efficient and eco-friendly manner. At the core of the process is a proprietary smelting technology that enables the company to smelt aluminum at a significantly lower temperature than traditional methods, resulting in a dramatic reduction in energy consumption and greenhouse gas emissions.The technology also allows for the recovery of valuable by-products, such as aluminum oxide and carbon, which can be reused and recycled. This not only reduces waste and improves sustainability, but also helps to keep costs down for the company’s customers.Along with the advanced smelting technology, Aluminum Smelting Equipment Company has also invested heavily in the development of state-of-the-art equipment to support the new process. This includes furnaces, casting machines, and other specialized equipment that have been specifically designed to work seamlessly with the company’s proprietary smelting technology.Combined, the new smelting process and equipment deliver a range of benefits for the company’s customers. For one, it allows for faster, more efficient production of high-quality aluminum, without sacrificing sustainability or safety. This is especially important in an industry that is becoming increasingly competitive, and where margins are often tight.The new process also reduces costs, both in terms of energy consumption and material waste, while also providing customers with access to valuable by-products that can be reused or sold. For companies that are looking to improve their bottom line and enhance their environmental credentials, this is a game-changer.In addition to the technical innovations, Aluminum Smelting Equipment Company has also invested in its people to ensure that they have the skills and expertise needed to operate the new process and equipment effectively. The company’s workforce includes highly skilled engineers, technicians, and other professionals who work closely with customers to design and implement customized solutions that meet their specific needs.Aluminum Smelting Equipment Company is not only committed to delivering exceptional products and services, but also to making a positive impact on the communities in which it operates. The company operates with a strong sense of environmental and social responsibility, and actively works to minimize its footprint and improve the lives of those around it.Overall, the introduction of the new smelting process represents a significant milestone for Aluminum Smelting Equipment Company. With its advanced technology, state-of-the-art equipment, and commitment to sustainability and social responsibility, the company is well-positioned to continue driving innovation in the aluminum industry and delivering value to its customers for years to come.
Melting Induction Furnaces: Efficient Iron Melting Solutions
Iron Melting Induction Furnace Revolutionizes the Foundry IndustryThe foundry industry is an essential part of the global manufacturing sector, providing metal castings for a variety of industries, including automotive, aerospace, and construction. Iron is one of the most commonly used metals in this sector, and its melting is a crucial step in the casting process. Traditionally, iron melting has been done using fossil fuel-fired cupolas, which have significant environmental and health risks. However, thanks to the power of innovation and technology, a new and more efficient iron melting solution has emerged- Iron Melting Induction Furnaces.One company in particular (need remove brand name) has been making waves in this space, offering cutting-edge products that set a new standard for efficiency, reliability, and environmental sustainability. Their Iron Melting Induction Furnaces have been recognized by foundry operators as game-changing technology that vastly improves the melting process and reduces operating costs.The technology behind these furnaces is based on the principle of electromagnetic induction, where an alternating electric current generates magnetic fields that heat the metal in the crucible. Compared to traditional cupolas, iron melting induction furnaces have several advantages, including:• Faster Melting Time - Induction furnaces can melt iron in less than an hour, compared to several hours in a cupola furnace.• Cleaner Process - Induction melting does not use coke as fuel, eliminating the harmful emissions and pollution associated with cupolas.• Smaller Footprint - Induction furnaces require less floor space compared to cupolas, making them more suitable for small and medium-sized foundries.• Efficient Energy Use - Induction furnaces are highly energy-efficient, leading to significant cost savings and reduced carbon footprint.The (Need remove brand name) Iron Melting Induction Furnaces combine these benefits and go further by providing customizable solutions for specific foundry needs. Their furnace systems range from small portable models for hobbyists and small foundries to larger, fully automated solutions for high-volume production environments.Moreover, the company's furnaces are designed to be user-friendly, with easy-to-use digital interfaces that allow operators to monitor and control the melting process precisely. The company also provides training and after-sales service to ensure that their customers get the most value from their investment."The Iron Melting Induction Furnace is a revolutionary technology that is transforming the foundry industry," notes (Need remove brand name) company spokesperson. "Our goal has always been to provide cost-effective and environmentally sustainable solutions to our customers, and these furnaces accomplish both. By leveraging the power of electromagnetic induction, we've created a smarter and cleaner way to melt iron that saves time, space, and energy, without compromising on quality."As a result of these innovations, the iron melting induction furnace market is expected to grow rapidly in the coming years, as more foundries realize the benefits of this technology. According to a recent industry report, the iron melting induction furnace market is projected to reach $1.5 billion by 2026, growing at a CAGR of 6.5% from 2021 to 2026.In conclusion, the Iron Melting Induction Furnace is a transformative technology that is changing the face of the foundry industry. With its many advantages, including faster melting time, cleaner process, smaller footprint, and energy-efficient use, this technology is making iron melting more accessible and sustainable for foundries of all sizes. As (Need remove brand name) continues to lead the way in this space, we can expect to see more innovations that help foundries become more efficient, cost-effective, and environmentally sustainable.
Top Zinc Melting Furnace Factories: Discover the Best Manufacturers in the Industry
Title: Advancements in Zinc Melting Furnace Technology Revolutionize the IndustryIntroduction:Zinc melting furnace factories play a crucial role in the manufacturing process of various industries, including automotive, construction, and electronics. These factories are responsible for melting and refining zinc to its molten form, which is then used for various applications. With technological advancements, several manufacturers have made significant strides in improving these furnaces' efficiency, safety, and environmental impact. In this article, we explore the recent developments in zinc melting furnace technology and their impact on the industry.1. Enhanced Efficiency through Innovative Designs:Leading zinc melting furnace manufacturers have been focusing on improving efficiency to meet the growing demands of zinc-consuming industries. They have developed advanced designs that optimize heat transfer, resulting in faster and more efficient melting processes. These innovative designs utilize various methods such as induction heating, electric resistive heating, or fossil fuel combustion to achieve optimal melting conditions.Furthermore, precise temperature control mechanisms and advanced insulation materials have been integrated into these furnaces, minimizing heat loss and enabling uniform melting throughout the entire process. As a result, manufacturers can achieve higher throughput capacities while reducing energy consumption, ultimately leading to cost savings and increased productivity.2. Emphasis on Safety Measures:Ensuring worker safety is of utmost importance in zinc melting furnace factories. Recent advancements have brought forth enhanced safety features, making the operating environment safer for workers. Furnaces now come equipped with sensor-based systems that continuously monitor various parameters like temperature, pressure, and gas leakage. In the event of any abnormalities or hazardous situations, these systems can automatically shut down the furnace or trigger alarms, thereby preventing accidents and ensuring a secure work environment.Moreover, improved ventilation and exhaust systems have been implemented to minimize the health risks associated with exposure to metal fumes and other harmful byproducts generated during the melting process. These advancements have significantly reduced the health hazards for workers, leading to improved overall well-being and better work conditions.3. Environmental Sustainability:Zinc melting furnace factories have made notable progress in reducing their environmental footprint. Manufacturers have adopted cleaner and more sustainable energy sources, such as electricity from renewable sources or use of cleaner fuels like natural gas, minimizing greenhouse gas emissions. Additionally, advanced filtration systems have been introduced to capture and treat harmful byproducts like particulate matter, sulfur dioxide, and nitrogen oxides generated during the melting process.Furthermore, recycling initiatives have gained momentum, allowing for the recycling and reuse of zinc scrap and dross generated during the manufacturing process. This significantly reduces waste disposal, conserves natural resources, and promotes a circular economy approach.Conclusion:Recent advancements in zinc melting furnace technology have revolutionized the industry, bringing forth numerous benefits such as enhanced efficiency, improved safety measures, and a reduced environmental impact. The integration of innovative designs, refined temperature control mechanisms, and advanced safety features have enabled manufacturers to achieve higher productivity while safeguarding the well-being of workers. Moreover, the adoption of sustainable practices, including the use of cleaner energy sources and recycling initiatives, have promoted environmental sustainability within the industry.As the demand for zinc in various industries continues to grow, it is encouraging to witness the continuous efforts made by zinc melting furnace factories to push the boundaries of technological innovation. These advancements not only contribute to the industry's growth but also address the pressing concerns of efficiency, safety, and sustainability.
Top Suppliers of Induction Furnace Cooling Systems" can be rewritten as "Best Induction Furnace Cooling System Suppliers" by removing the brand name.
Induction Furnace Cooling System Supplier Announces New Product LineInduction furnace cooling system supplier, [brand name removed], is proud to announce the launch of its new line of advanced cooling systems. The new product line promises to deliver superior performance, efficiency, and durability to clients in the metal fabrication industry.The cooling systems have been designed to enhance the performance and lifespan of induction furnaces. They have been engineered with cutting-edge technologies that ensure efficient heat transfer and reduce energy consumption. The systems also feature several safety mechanisms, including flameproof control panels and automatic shut-off valves that protect the furnaces and environments against damage or accidents.At [brand name removed], we take pride in delivering high-quality, reliable, and innovative solutions to our clients," said the company's spokesperson. "The introduction of our new product line reflects our commitment to meeting the needs of our clients, improving their processes, and enhancing their bottom line."The new cooling systems are suitable for various applications, including steel mills, foundries, and metal fabrication workshops. They are compatible with different types of induction furnaces, including coreless, channel, and crucible furnaces. The systems come in different sizes, capacities, and configurations, to cater to the unique needs of each client."We understand that each client has unique requirements, and that's why we offer customized solutions that meet their specific needs," added the spokesperson. "Our team of experts is always available to provide technical support and advice to our clients, from the initial consultations, installation, testing to after-sales services."The launch of the new product line follows a rigorous research and development process, which involved extensive testing, prototyping, and refinement. The team of engineers, scientists, and technicians also collaborated with clients to understand their needs and challenges and incorporate their feedback into the products' design.The company's multi-disciplinary team comprises experts in various fields, including engineering, materials science, fluid dynamics, and process control. The team is continuously exploring new technologies and materials that can enhance the product's performance, reduce costs, and improve sustainability."We recognize that innovation is a continuous process, and we are constantly seeking to improve our products and services. We also prioritize sustainability and eco-friendliness in our operations, which is why our products are designed with energy-efficient technologies, reduce waste and emissions, and use eco-friendly materials," said the spokesperson.In addition to the new product line, the company offers a broad range of services, including installation, maintenance, repair, and replacement of induction furnace cooling systems. They also provide training and technical support to their clients' personnel to enable them to operate and maintain the systems effectively."We provide a one-stop-shop for all our clients' needs and ensure that they get superior quality products and services at competitive prices. Our goal is to establish long-term relationships with our clients, based on trust, reliability, and mutual growth," concluded the spokesperson.In conclusion, [brand name removed], the induction furnace cooling system supplier, has launched a new line of efficient, durable, and safe cooling systems that are suitable for various metal fabrication applications. The products have been designed with innovative technologies, safety features, and eco-friendly materials to enhance the performance of induction furnaces, reduce energy consumption, and protect environments and personnel. The company also offers a broad range of services, including installation, maintenance, repair, and replacement of cooling systems, and technical support to clients' personnel.
Top Electric Lead Melting Furnace Supplier for Optimal Performance
Best Electric Lead Melting Furnace Supplier Revolutionizes the IndustryAs the demand for sustainable and environmentally friendly practices continues to grow, the need for efficient and reliable lead melting furnaces has become increasingly important. With a commitment to innovation and cutting-edge technology, one company has emerged as the industry leader in providing top-notch electric lead melting furnaces. Leveraging their expertise and dedication to customer satisfaction, this supplier has revolutionized the lead melting furnace industry.Founded in [year], this renowned company has built a solid reputation by consistently delivering high-quality products and unparalleled service to their customers. With a strong focus on research and development, they continuously strive to improve and enhance their electric lead melting furnaces, setting new industry standards.The company's electric lead melting furnaces are carefully designed to meet the specific requirements of various industries, including battery manufacturing, ammunition production, and various other lead-based applications. By using cutting-edge technology, their furnaces are not only energy-efficient but also cost-effective for businesses.Efficiency is a key aspect of the company's furnaces. Equipped with state-of-the-art heating elements, their electric lead melting furnaces offer rapid and uniform heating, ensuring optimal melting and refining processes. This efficiency not only saves time but also promotes higher productivity in lead-based industries.One of the most significant advantages of the company's electric lead melting furnaces is their commitment to sustainability. The furnaces are designed to minimize carbon emissions and energy consumption, making them environmentally friendly. This approach aligns with the global movement towards greener solutions and ensures compliance with stringent environmental regulations.Moreover, the electric lead melting furnaces offered by this supplier are also highly durable and require minimal maintenance. The company prides itself on manufacturing robust and long-lasting furnaces, ensuring that their customers receive reliable equipment that withstands heavy usage. This durability significantly reduces overall operating costs for businesses, making it a financially viable choice for both small and large enterprises.In addition to their exceptional products, customer satisfaction is at the core of this supplier's business philosophy. Their dedicated customer support team works closely with clients to understand their specific requirements and provide personalized solutions. By offering comprehensive pre-sales and after-sales support, they ensure that customers receive the assistance they need at every step of the way.To further enhance customer experience, the company provides regular training programs to help users optimize the efficiency and productivity of their electric lead melting furnaces. They believe that by empowering their customers with knowledge and skills, they can truly maximize the benefits of their equipment.The company's commitment to quality and innovation has garnered them a prestigious reputation in the industry. They are recognized worldwide as a leading supplier of electric lead melting furnaces, trusted by businesses across various sectors. With a strong global presence and a vast network of partners, they cater to customers around the globe, delivering excellence in every furnace they offer.In conclusion, this renowned electric lead melting furnace supplier has revolutionized the industry through their commitment to innovation, sustainability, and customer satisfaction. With their cutting-edge technology, efficient performance, and environmentally friendly approach, they have set new industry benchmarks for electric lead melting furnaces. As businesses strive to reduce their environmental footprint and improve efficiency, this supplier's reliable and top-notch furnaces serve as the ideal solution for a wide range of industries.
Top Copper Scrap Melting Furnace Manufacturers
Title: Prominent Copper Scrap Melting Furnace Manufacturers Emerge in the MarketIntroduction:The growing demand for copper, coupled with the emphasis on sustainable practices, has fueled the need for advanced technology in the recycling industry. Leading manufacturers are stepping up to meet this demand by developing innovative copper scrap melting furnaces. With a focus on energy efficiency, productivity, and environmental conservation, these manufacturers are revolutionizing the copper recycling industry. This article will highlight some of the best copper scrap melting furnace manufacturers who are making significant strides in the market.1. Company A:Company A has emerged as a force to be reckoned with in the copper scrap melting furnace market. Utilizing state-of-the-art technology, their furnaces are designed to maximize energy efficiency while minimizing emissions. The company's commitment to sustainable practices is evident through their incorporation of advanced filtration systems, resulting in reduced air pollution.With a strong track record in the industry, the company has earned a solid reputation for producing reliable and durable copper scrap melting furnaces. Moreover, Company A places a strong emphasis on customer satisfaction by offering comprehensive customer support and maintenance services, ensuring seamless operations for their clientele.2. Company B:Company B prides itself on its ability to offer tailored solutions to meet specific customer requirements. Their copper scrap melting furnaces are customizable, allowing businesses to optimize their operations to suit their specific needs. Recognizing the importance of efficiency and cost-effectiveness, Company B has incorporated cutting-edge technology into their designs to enhance productivity while minimizing energy consumption.The company's commitment to quality is further reflected in their attention to detail during the manufacturing process. Each furnace undergoes rigorous testing, ensuring that only top-notch products reach the market. Customer feedback plays a significant role in their continuous improvement strategy, allowing Company B to constantly innovate and enhance their offerings.3. Company C:Company C sets itself apart by combining years of experience with a commitment to sustainability. Their copper scrap melting furnaces are designed to exceed industry standards, utilizing advanced features such as intelligent automation and accurate temperature control. This results in optimized energy consumption and reduced waste generation during the melting process.The company's expertise in energy management and emissions control ensures compliance with environmental regulations. Additionally, Company C focuses on continuous research and development, incorporating the latest technological advancements into their products. This allows customers to benefit from enhanced efficiency, reduced downtime, and improved operational control.4. Company D:Company D has established a strong presence in the copper scrap melting furnace market by prioritizing customer-centric solutions. Their furnaces are engineered to deliver exceptional performance, catering to a broad range of customer requirements. By adopting a holistic approach, virtual simulations enable the company to offer innovative designs that optimize melting efficiency.Additionally, Company D offers comprehensive after-sales support, including installation, training, and maintenance services. Their commitment to service excellence has garnered them a loyal customer base and positioned them as a reliable partner in the copper recycling industry.Conclusion:The copper scrap melting furnace market has witnessed significant advancements from prominent manufacturers. Companies A, B, C, and D have demonstrated their commitment to sustainability, energy efficiency, and customer satisfaction. By offering innovative and customizable solutions, these manufacturers are leading the way in revolutionizing the copper recycling industry. With continued investment in research and development, these companies are sure to shape the future of copper scrap melting furnaces, further contributing to the circular economy.