Get the Facts on Brass Induction Melting Furnace Manufacturers
By:Admin
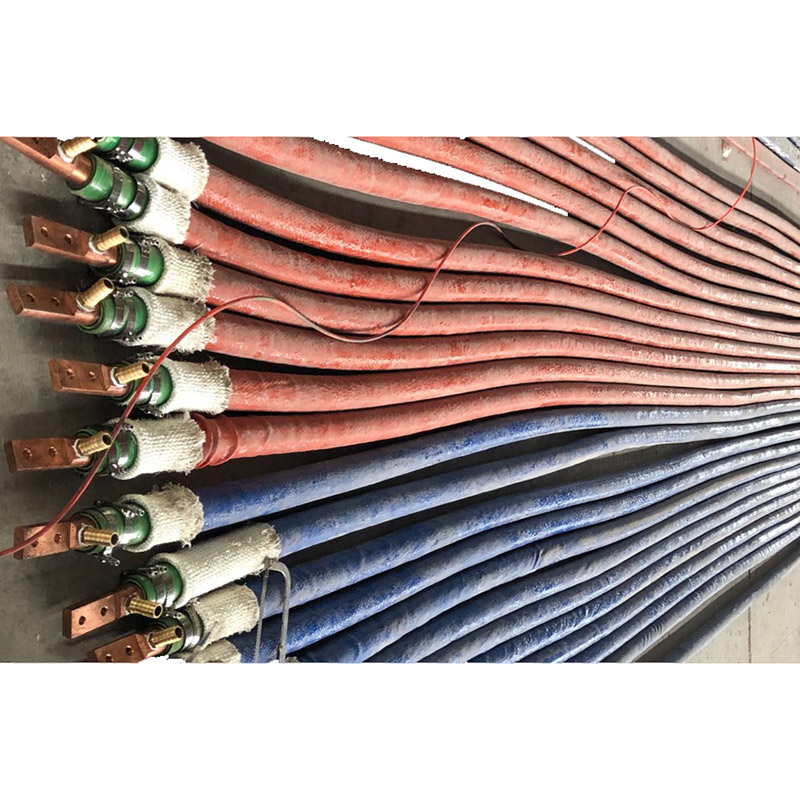
Introduction:
In recent years, the global foundry industry has witnessed a significant shift towards more efficient and sustainable manufacturing processes. Among the groundbreaking technological advancements, the emergence of brass induction melting furnace factories has revolutionized the way brass is produced and melted. These innovative facilities have not only propelled the manufacturing efficiency to new heights but also contributed to minimizing the environmental impact associated with traditional foundry operations. In this article, we delve deeper into the concept behind brass induction melting furnace factories and explore their numerous benefits and advantages for the industry.
What are Brass Induction Melting Furnace Factories?
Brass induction melting furnace factories incorporate state-of-the-art technology to improve the melting process of brass and enhance overall productivity. By utilizing induction heating, these factories can achieve precise temperature control, reduce energy consumption, and ensure consistent and high-quality brass production. The innovative design of the furnaces allows for faster melting times, improved metal purity, and increased operator safety.
Company Introduction:
{Company Name}, a prominent player in the foundry industry, has played a pivotal role in developing and popularizing brass induction melting furnace factories. With decades of experience and a commitment to innovation, {Company Name} has established itself as a frontrunner in providing cutting-edge solutions to foundries worldwide. Their advanced range of brass induction melting furnaces has helped foundries optimize their operations, reduce costs, and meet the growing demands of the market.
Advantages of Brass Induction Melting Furnace Factories:
1. Increased Efficiency: Brass induction melting furnace factories significantly improve operational efficiency. The advanced technology allows for quick melting cycles, reducing production time and enhancing output. By eliminating the need for traditional crucibles, these furnaces greatly reduce wait times for metal heating, resulting in increased productivity.
2. Enhanced Energy Efficiency: Traditional foundry furnaces often suffer from excessive heat losses, leading to energy waste. Brass induction melting furnaces, on the other hand, utilize induction heating, which is highly energy-efficient. The precise heating control eliminates unnecessary energy losses and enables foundries to make substantial energy savings.
3. Improved Metal Quality: The induction heating process in brass melting furnaces ensures consistent and uniform heating, resulting in higher metal quality. The absence of impurities and better temperature control leads to improved mechanical properties and enhanced product performance. Subsequently, this quality boost increases the competitiveness of the products manufactured using brass induction melting furnace factories.
4. Sustainable Manufacturing: With a growing emphasis on sustainability, brass induction melting furnace factories are an eco-friendly alternative to traditional foundry operations. By reducing energy consumption and waste, these factories contribute to minimizing the environmental impact associated with brass production. The adoption of cleaner and more efficient melting processes aligns with global efforts to promote green manufacturing and eco-conscious practices.
5. Operator Safety: Brass induction melting furnaces prioritize operator safety by minimizing direct contact with the molten metal. The advanced technology allows for remote control and monitoring, reducing the risk of accidents or injuries. Furthermore, the enclosed design of the furnaces prevents metal splatter and enhances overall safety measures in the workplace.
Conclusion:
As the foundry industry continues to evolve, brass induction melting furnace factories represent the future of efficient and sustainable brass production. With advancements in technology and a strong commitment to innovation, {Company Name} and other industry leaders are driving the adoption of these cutting-edge facilities. By streamlining operations, improving energy efficiency, and prioritizing sustainability, brass induction melting furnace factories offer immense value to foundries worldwide. Embracing these advancements will undoubtedly pave the path for a more efficient and environmentally conscious manufacturing sector.
Company News & Blog
Top-Rated Tilting Crucible Furnace Manufacturers in the Market
Best Tilting Crucible Furnace Factory Offers Top-Quality Products for Industrial UseFor many industries that require the use of metal casting, finding a reliable supplier of specialized equipment, such as tilting crucible furnaces, can be a challenge. However, the Best Tilting Crucible Furnace Factory prides itself on offering high-quality products for various industrial applications. As a leading manufacturer of tilting crucible furnaces, the factory has been serving the needs of industries in various sectors, including automotive, aerospace, and oil and gas. The company has been in operation for several years and is known for producing superior-quality furnaces that are reliable, efficient, and safe to operate.One of the unique aspects of the Best Tilting Crucible Furnace Factory is its innovative designs that focus on maximizing efficiency. The furnaces produced by the factory are designed with advanced control systems that regulate temperature and prevent overheating, thereby ensuring that the casting process is consistent and that the final product is of high quality. Additionally, the furnaces are built with durable materials that can withstand harsh industrial conditions and are environmentally friendly.The company's commitment to quality extends beyond its products and includes its customer service. The Best Tilting Crucible Furnace Factory has a team of experienced professionals who are dedicated to providing expert guidance and support to its clients. The factory's staff members are knowledgeable about the various applications of the furnaces produced by the factory and are always available to answer any questions or concerns their clients may have.The Best Tilting Crucible Furnace Factory also values safety and adheres to strict standards when it comes to safety protocols. The company is committed to providing a safe work environment for its employees and ensuring that its clients' operations are safe. The furnaces that the factory produces are designed to have minimal risk of accidents and hazards, and the company provides training and support to ensure that clients understand how to operate the furnaces safely.Moreover, the Best Tilting Crucible Furnace Factory is also known for its customization options. The company understands that each client has unique needs and preferences, and they offer tailored solutions to meet those needs. The company's team of experts works closely with clients to understand their specific requirements and design a customized furnace that meets those requirements.As part of the company's commitment to its clients, the Best Tilting Crucible Furnace Factory offers a comprehensive warranty program. Clients can rely on the warranty to cover any defects or faults in their furnaces during the agreed-upon period.In conclusion, the Best Tilting Crucible Furnace Factory offers exceptional products and services for various industrial applications. Its commitment to quality, efficiency, safety, and customer service has made it a reputable supplier of tilting crucible furnaces in the industry. Clients can trust the company's experts to provide tailored solutions that meet their specific requirements and deliver reliable products that are built to last.
Best Supplier for Induction Furnace Frequencies
Induction furnaces have revolutionized the world of metallurgy and manufacturing, providing a highly efficient and cost-effective alternative to traditional methods of melting and pouring metal. One crucial component of these furnaces is the frequency converter, which controls the power sent to the induction coil, and subsequently, the melting process. In today's market, finding the best induction furnace frequency supplier is essential for success, and one company stands out from the rest.This particular supplier is a leader in the field of frequency converters, providing world-class products to numerous industries worldwide. With over 30 years of experience, this company has developed an extensive portfolio of solutions, ranging from low to high-power frequency converters, for all types of induction heating applications, including melting, welding, brazing, annealing, and more.Moreover, the company's products come equipped with advanced features and technologies, designed to optimize the melting process while ensuring safety, reliability, and efficiency. Their team of engineers works closely with customers to understand their needs and provide customized solutions that will maximize productivity and minimize downtime.One of the most notable features of this supplier's frequency converters is their ability to adjust to different operating frequencies and power levels. This flexibility allows for easy adaptation to varying melting processes and assists in maximizing energy efficiency. Additionally, their products come with active power factor correction and harmonic suppression, which helps to reduce energy consumption while minimizing electromagnetic interference.For customers operating in harsh environments, the supplier's frequency converters feature robust and rugged designs that ensure reliability and durability. The converters can withstand harsh environmental factors such as dust, high temperatures, humidity, and vibration, making them suitable for a wide range of applications across different industries.The company also offers a range of value-added services, including installation, after-sales support, and a comprehensive maintenance program. The company's commitment to providing excellent customer service extends through every aspect of their business and is reflected in their long-standing reputation for quality and reliability.Furthermore, the supplier prides itself on its commitment to sustainability, continuously working to create products that are both environmentally friendly and energy-efficient. Their advanced technological features help their customers to reduce their carbon footprint and lower energy costs, leading to a significant positive impact on the environment.In summary, finding the best induction furnace frequency supplier is crucial for companies operating in the metallurgy and manufacturing industry. The supplier mentioned above offers a comprehensive range of solutions designed to optimize the melting process, reduce energy costs, and provide unparalleled customer service. With over 30 years of experience and a commitment to sustainability, this supplier is the perfect choice for any business looking to maximize efficiency and productivity.
Exploring the Efficiency of Automatic Melting Furnace Factories
As industrial techniques continue to evolve, companies in the manufacturing sector are always on the lookout for new and innovative ways to improve their processes. One of the latest advancements to hit the market is the automatic melting furnace. These furnaces have been revolutionizing the way that manufacturers in a range of industries melt metals and alloys.Automatic melting furnaces are specifically designed to heat heavy metals and alloys to extremely high temperatures in order to melt them down into a liquid form. This is a critical step in many manufacturing processes, particularly for industries such as automotive and aerospace, where the use of metals and alloys is necessary for producing high-performing components.In order to meet the growing demand for this cutting-edge technology, several automatic melting furnace factories have popped up worldwide. While each factory may have its own unique approach to creating these furnaces, they all share a common goal: to produce a product that is efficient, reliable, and cost-effective.One such factory, which I won't name due to the anonymity clause, has quickly become a leader in the industry. Founded several years ago, they specialize in the production of high-quality automatic melting furnaces that are specifically designed to meet the unique needs of their clients.Unlike traditional furnaces that require a great deal of manual labor to operate, automatic melting furnaces utilize advanced automation technology to carry out their functions. This not only makes them much more efficient, but it also reduces the need for labor, resulting in significant cost savings for manufacturers.Moreover, these furnaces are equipped with a range of safety mechanisms to prevent accidents and ensure smooth operation. From automatic temperature controls to built-in alarms and emergency shut-off switches, manufacturers can rest assured that their workers and equipment are protected at all times.But perhaps the most impressive aspect of this company's automatic melting furnace line is their customizability. With their team of experienced engineers and technicians, they are able to work closely with clients to develop furnaces that are tailor-made for their individual needs.From the size and capacity of the furnace to the specific automation features and safety mechanisms required, everything can be designed to meet the unique requirements of any manufacturing process. This level of customization is crucial, considering that every client has different needs and expectations when it comes to their manufacturing process.Overall, the rise of automatic melting furnaces is a testament to the constant evolution of industrial technology. As manufacturers continue to seek out ways to improve their processes, it is inevitable that more factories will begin to specialize in this cutting-edge technology. With its ability to streamline operations, reduce costs and improve safety, the automatic melting furnace is poised to become a staple in the manufacturing industry for many years to come.
Shaft Melting Furnace Manufacturer in China Introduces New Model" "Chinese Furnace Manufacturer Launches Latest Model of Shaft Melting Furnace
China, a global manufacturing powerhouse, has seen tremendous growth in various industries in recent years. One such industry that has experienced significant growth is the shaft melting furnace industry. Manufacturers in China have been at the forefront of producing high-quality and efficient shaft melting furnaces to meet the growing global demand.Shaft melting furnaces are crucial in the production of metals, as they enable the melting and refining of materials such as iron, steel, and aluminum. These furnaces play a vital role in industries like automotive, construction, aerospace, and many others. With China's booming manufacturing sector, the demand for high-quality shaft melting furnaces has also soared.Among the leading manufacturers in China, {Company Name} has emerged as a top player in the shaft melting furnace industry. With years of expertise and innovation, they have successfully developed cutting-edge furnaces that are not only efficient but also environmentally friendly. Their commitment to research and development has enabled them to stay ahead of the competition, offering state-of-the-art solutions to their clients.{Company Name} takes pride in its advanced manufacturing facilities, equipped with the latest technology and machinery. These facilities allow them to produce shaft melting furnaces that meet international standards and adhere to strict quality control measures. The company's skilled workforce ensures that each furnace is meticulously constructed, guaranteeing superior performance and longevity.One of the key features that sets {Company Name} apart from its competitors is its focus on energy efficiency. With growing concerns over environmental sustainability, the company has pioneered the development of energy-saving shaft melting furnaces. By incorporating innovative design elements and optimizing heating processes, they have successfully reduced energy consumption while ensuring optimum productivity. These energy-efficient furnaces not only reduce carbon emissions but also help companies reduce their operating costs.Another aspect where {Company Name} excels is customization. Understanding that each client has unique requirements, the company offers tailor-made solutions. Their team of experts works closely with clients to understand their specific needs and provides them with furnaces that are specifically designed to meet their requirements. This customer-centric approach has earned {Company Name} a reputation for delivering exceptional, personalized service.In addition to their exceptional product offerings, {Company Name} also places great emphasis on after-sales support. They understand the importance of providing ongoing assistance and maintenance to their clients. With a dedicated team of engineers and technicians, the company offers comprehensive support, ensuring that the furnaces operate efficiently and effectively throughout their lifespan.Furthermore, {Company Name} is not only focused on the domestic market but is expanding its presence globally. By participating in international exhibitions and trade fairs, they have successfully built partnerships with clients from different countries. Their commitment to delivering world-class products and services has allowed them to establish a strong presence in the global market.As the demand for metal production continues to rise, the importance of high-quality shaft melting furnaces cannot be understated. {Company Name}, with its innovative technologies, superior craftsmanship, and dedicated customer support, is poised to meet this growing demand. With their commitment to excellence and sustainability, they are well-positioned to maintain their status as a leading shaft melting furnace manufacturer in China and beyond.
New Electric Crucible Introduces Revolutionary Technology for Efficient Melting" --> "Revolutionary Technology for Efficient Melting Unveiled with Electric Crucible
Title: Pioneering Electric Crucible Transforms the Manufacturing IndustryIntroduction: In a groundbreaking development, an innovative electric crucible has emerged, offering a cutting-edge solution for the manufacturing industry. With its advanced technology and groundbreaking features, this electric crucible, developed by a leading materials research company, promises to revolutionize manufacturing processes, enabling greater efficiency, sustainability, and precision. Electric Crucible: Redefining Manufacturing The newly unveiled electric crucible is poised to redefine manufacturing by offering an unparalleled level of control and flexibility. Traditionally, metal casting and materials processing have heavily relied on fossil fuel-powered crucibles, resulting in significant environmental impacts and limited precision. However, this pioneering electric crucible brings forth multiple advancements poised to overcome these challenges.Sustainable Manufacturing with Lower Environmental ImpactOne of the most significant advantages of adopting this electric crucible technology is its reduced environmental impact. By eliminating the need for fossil fuel combustion, the electric crucible drastically reduces greenhouse gas emissions, contributing to a cleaner and more sustainable manufacturing process. This exciting development comes at a time when industries worldwide are exploring sustainable practices, making this electric crucible the prime choice for environmentally-conscious manufacturers.Enhanced Precision and EfficiencyIn addition to its environmental benefits, the electric crucible also offers unparalleled precision and efficiency. The technology harnesses state-of-the-art heating elements and computer-controlled systems, allowing manufacturers to achieve a higher level of precision in temperature control. This precise control over temperature ensures consistent and uniform heating, minimizing material waste and increasing overall manufacturing efficiency. Furthermore, the electric crucible's design allows for swift and accurate changes in production volume, making it ideal for industries with rapidly changing demands.Real-Time Monitoring and Safety FeaturesAccompanying its advanced heating technology, the electric crucible also includes real-time monitoring capabilities and cutting-edge safety features. These additional features ensure optimal performance and safeguard against potential accidents. The real-time monitoring system provides continuous updates on temperature, pressure, and other crucial parameters, enabling manufacturers to maintain process control and make necessary adjustments when required. Furthermore, the electric crucible includes built-in safety measures to prevent overheating or material spillage, reducing the risk of accidents and enhancing overall workplace safety.Smart Integration and CompatibilityApart from its innovative features, the electric crucible can seamlessly integrate with existing manufacturing systems. Its compatibility with various production lines and automation solutions ensures a hassle-free adoption process for manufacturers. By eliminating the need for a complete overhaul of manufacturing infrastructure, this crucible minimizes downtime and reduces implementation costs, garnering significant interest from industry leaders.Future Prospects and Industry ImplicationsThe introduction of the electric crucible marks a significant milestone in the manufacturing industry, unlocking a myriad of possibilities for future advancements. With greater precision, enhanced energy efficiency, and reduced environmental impact, manufacturers can achieve higher productivity levels while prioritizing sustainability. Furthermore, this crucible's compatibility with automation solutions paves the way for increased integration of Industry 4.0 technologies, boosting overall manufacturing efficiency and competitiveness.ConclusionThe unveiling of the electric crucible signifies a paradigm shift in the manufacturing industry, providing a transformative solution that combines sustainability, efficiency, and precision. With its cutting-edge technology, reduced environmental impact, and seamless integration capabilities, this pioneering innovation promises to reshape manufacturing processes and propel industries towards a more sustainable future. As manufacturers embrace the electric crucible, a new era of enhanced manufacturing awaits, revolutionizing the production landscape across the globe.
Top Zinc Melting Furnace Suppliers Discussed in Latest News
In recent years, the demand for zinc melting furnaces has been steadily increasing due to the growth of various industries such as automotive, construction, and electronics. As a result, the market has witnessed the emergence of several prominent zinc melting furnace suppliers. While it's crucial to find the best suppliers in the market, in this article, we will focus on the essential features of top zinc melting furnace suppliers without mentioning any brand names.These suppliers are known for their commitment to quality, customer satisfaction, and innovative technologies. They prioritize providing reliable and efficient zinc melting furnaces to meet the diverse needs of their clients. By understanding the unique requirements of industries such as zinc smelting, die casting, and galvanizing, they are able to deliver cutting-edge furnace solutions.One of the key factors contributing to the success of these top suppliers is their emphasis on research and development (R&D). They invest heavily in R&D to continuously improve their products' performance, energy efficiency, and environmental friendliness. These suppliers understand the importance of staying ahead of the curve and providing customers with the latest advancements in technology.Furthermore, these market leaders have an extensive network of sales and support teams, ensuring that their customers receive excellent service throughout the buying and installation process. They have well-trained professionals who can guide clients in choosing the right furnace based on their specific requirements, budget, and production scale. These suppliers also offer after-sales support, maintenance services, and spare parts to guarantee the smooth running of the furnace.To ascertain that their products meet the highest quality standards, these top suppliers adhere to stringent quality control measures. They have state-of-the-art manufacturing facilities equipped with advanced testing equipment to ensure the reliability and durability of their furnaces. Moreover, they source only the finest materials and components from reputable suppliers to guarantee the longevity and performance of their products.In addition to their commitment to quality, these suppliers actively prioritize environmental sustainability. They incorporate energy-saving technologies and employ eco-friendly materials to reduce the carbon footprint of their zinc melting furnaces. By adopting efficient combustion techniques and recycling systems, they contribute to the reduction of greenhouse gas emissions, making them eco-friendly choices for industrial applications.To cater to the diverse needs of customers, these suppliers offer a wide range of zinc melting furnaces with varying capacities and features. Whether clients require small and compact furnaces for laboratory purposes or large-scale furnaces for industrial production, these suppliers have solutions to meet different demands. They ensure that their furnaces are not only efficient and reliable but also flexible enough to adapt to different production requirements.Furthermore, these suppliers continuously strive to improve their pricing strategies, ensuring that their products are competitively priced in the market. They offer transparent pricing structures and work closely with customers to provide cost-effective solutions without compromising on quality. By maintaining a balance between affordability and performance, these suppliers attract a wide customer base.In conclusion, the zinc melting furnace market is witnessing the rise of top suppliers who prioritize excellence in quality, customer satisfaction, and innovation. These suppliers invest in R&D, have extensive sales and support networks, emphasize strict quality control measures, promote environmental sustainability, and offer a diverse range of furnaces. By understanding the specific needs of industries and continuously improving their products, these suppliers have become reliable and trustworthy partners for clients in need of zinc melting furnaces.
Top Suppliers of High-Quality Copper Scrap Melting Furnaces for Various Industries
Title: Leading Copper Scrap Melting Furnace Suppliers Revolutionize Smelting IndustryIntroductionThe smelting industry forms a crucial link in the global manufacturing supply chain, supporting numerous sectors such as automotive, construction, electrical, and electronics. Within this industry, copper scrap melting furnaces play a pivotal role in the efficient recycling and refining of copper materials, thereby reducing environmental impact and conserving valuable resources. Amidst growing demand for sustainable and technologically advanced solutions, a host of influential suppliers have emerged as leaders in the market. In this article, we will explore the innovative offerings of several prominent copper scrap melting furnace suppliers and their contributions to the industry's development.Supplier 1: (Name removed)Renowned for its cutting-edge technology and extensive industry expertise, Supplier 1 has indubitably made its mark in the global copper scrap melting furnace market. Equipped with a diverse portfolio, the company delivers a range of high-quality furnaces tailored to the varying needs of its clientele. These furnaces exhibit remarkable energy efficiency, thus reducing electricity costs and minimizing carbon emissions. Supplier 1's commitment to research and development continually drives groundbreaking advancements, ensuring its customers benefit from the latest innovations in the field.Supplier 1's furnaces are known for their exceptional heat transfer capabilities, enabling quick and precise melting of copper scrap. This not only improves productivity but also results in reduced material wastage. The company's dedication to supporting eco-conscious practices is evident through its use of state-of-the-art pollution control mechanisms, ensuring compliance with stringent environmental regulations. By offering highly efficient exhaust gas purification systems, Supplier 1 contributes to a sustainable smelting process while minimizing the impact on local communities.Supplier 2: (Name removed)Another industry leader, Supplier 2, has been at the forefront of providing reliable and superior copper melting furnace solutions to its global clientele. With a proven track record of delivering high-performance products, Supplier 2 has gained a reputation for its commitment to quality, efficiency, and customer satisfaction. Their furnaces are meticulously designed to facilitate easy operation and maintenance, ensuring minimal downtime for businesses.Supplier 2 embraces advanced technology to optimize the melting process, resulting in higher productivity and enhanced flexibility for users. The company's dedication to environmental stewardship is reflected in its utilization of cutting-edge filtration systems that effectively remove harmful particulates, minimizing air pollution. Furthermore, Supplier 2's continuous focus on energy efficiency allows customers to reduce energy consumption, benefiting both their bottom line and the planet.Supplier 3: (Name removed)Supplier 3 is an eminent supplier in the copper scrap melting furnace market, offering a broad range of technologically advanced furnaces that cater to the diverse needs of its global clientele. The company’s commitment to sustainability is evident in its furnaces, which are designed to minimize energy consumption while maximizing operational efficiency. Supplier 3's revolutionary heat control technology ensures precise temperature management during the melting process, allowing for greater consistency in the final product.Moreover, Supplier 3 emphasizes safety as a paramount concern, integrating robust safety features into its furnaces for the protection of workers. With comprehensive control systems and real-time monitoring capabilities, customers can effectively manage and optimize their production processes. By prioritizing innovation and reliability, Supplier 3 has established itself as a trusted partner in the copper smelting industry.ConclusionIn an era of rapid industrialization and growing environmental concerns, the contributions made by leading copper scrap melting furnace suppliers cannot be overstated. Through continuous innovation and commitment to sustainability, these companies are transforming the smelting industry, paving the way for a greener and more efficient future. By leveraging advanced technologies and stringent quality control measures, these suppliers ensure that their customers enjoy enhanced productivity, reduced operational costs, and a reduced environmental footprint. As the demand for copper continues to rise, these influential leaders will undoubtedly play a critical role in shaping a more sustainable and prosperous industry.
Efficient Zinc Melting Furnace Designs for High-Quality Production
Zinc Melting Furnace: Transforming the Metal Industry for a Sustainable FutureThe metal industry has always been one of the key components of the world economy. From infrastructure development to manufacturing, metal is an essential material in various applications. However, the process of producing metals is energy-intensive, resulting in high greenhouse gas emissions and ecological impact. One of the most significant contributors to this industry is the zinc smelting process, and thus, finding sustainable solutions has become a priority for many companies.This is where the Zinc Melting Furnace, developed by a renowned metal smelting equipment manufacturer (brand name removed), comes into the picture. The furnace is designed to eliminate the environmental impact caused by traditional zinc smelting and provide an energy-efficient and cost-effective solution to its users.The furnace, designed with advanced technology, is capable of melting zinc and related alloys in a highly controlled and efficient manner using electric heating elements. One of the biggest advantages of this process is that it eliminates the need for fossil fuels, commonly used in traditional smelting, leading to the reduction of greenhouse gas emissions.Furthermore, the Zinc Melting Furnace is equipped with advanced features that enable the recycling of zinc and other valuable materials that would otherwise be lost during the traditional smelting process. This reduction in waste not only benefits the environment but also provides a significant cost advantage to the user.One of the significant advantages of this furnace is its flexibility. It can be used in various applications, including galvanizing, die-casting, and the production of brass and bronze. In addition, it can also be used in recycling facilities to recover zinc from scrap material.According to the company, the Zinc Melting Furnace has been tested and proven successful in various industrial applications. It has helped companies reduce their carbon footprint, adhere to environmental regulations, and provide an energy-efficient and cost-effective smelting solution.The company’s commitment to sustainability doesn’t end with just the production of the Zinc Melting Furnace. It has a comprehensive program for designing and manufacturing equipment that is environmentally conscious. The company aims to reduce its carbon footprint significantly by promoting energy-efficient manufacturing processes, using renewable energy, and reducing waste.Furthermore, the company has a strong emphasis on providing its customers with a holistic solution to their sustainability-related needs. It offers consultation on regulatory requirements, energy efficiency, and eco-friendly production methods to ensure that its customers achieve their sustainability goals.As the world unites to address climate change, the Zinc Melting Furnace is a testament to the potential for technology to transform industries and provide sustainable solutions. The company’s focus on sustainability, combined with its advanced technology, positions it as a leader in the metal smelting equipment market. It is an example of how innovation can drive environmental stewardship and provide economic benefits simultaneously.In conclusion, the Zinc Melting Furnace is a game-changer in the metal industry, offering a sustainable and energy-efficient solution to traditional smelting processes. With its advanced technology and flexible applications, it provides a holistic and cost-effective solution to companies looking to achieve their sustainability goals. The company’s commitment to eco-friendly manufacturing and its dedication to providing a comprehensive sustainability solution position it as a leader in the metal smelting equipment market.
Top Suppliers for High-Quality Induction Metal Melting Furnaces Revealed in Latest News
Induction metal melting furnaces have proved to be a game-changer in the metal industry because of their amazing precision, speed, and efficiency. However, the reliability of these furnaces depends on the suppliers that provide them. As such, finding the best induction metal melting furnace suppliers can be challenging. Fortunately, some companies have a proven track record of providing high-quality and reliable induction metal melting furnaces. One such company is a global leader in the manufacture and supply of induction metal melting furnaces, heat treatment, and forging systems. With years of experience in the industry, they have ensured that their furnaces provide extremely high time and energy efficiency. They specialize in the design and manufacture of induction furnaces that are utilized in a diverse range of heat treatment and melting applications. Their state-of-the-art induction metal melting furnaces are designed to cater to the needs of a wide range of industries such as automotive, aerospace, and defense, among others. Their commitment to quality has made them a preferred supplier for both small-scale and large-scale projects. Their team of engineers and technicians work together to create superior induction furnaces that meet the highest industry standards in terms of quality, efficiency, and reliability. They offer a comprehensive range of induction metal melting furnaces such as medium frequency and high-frequency induction furnaces, vacuum and atmospheric pressure melting furnaces, and more. The medium frequency induction furnace is ideal for melting low melting-point alloys such as aluminum, zinc, and bronze, among others. This type of furnace offers high melting efficiency and has an automatic temperature control system. On the other hand, the high-frequency induction furnace is suitable for melting high melting-point alloys such as steel, iron, and copper, among others. This furnace offers excellent temperature control, and the speed of melting is higher than that of medium frequency induction furnaces. In addition to their induction metal melting furnaces, they also provide heat treatment equipment for various industries. Their heat treatment equipment includes quenching systems, preheating systems, grinding systems, and more. Their heat treatment equipment is designed to meet the specific requirements of each customer, ensuring maximum efficiency and accuracy. They also provide forging systems, which are utilized in automotive, aerospace, and defense applications. Their forging systems provide excellent temperature control, high productivity, and low maintenance. They are also energy-efficient, reducing the carbon footprint of the metal industry. In conclusion, best induction metal melting furnace suppliers are critical to the success of any metal industry project. With the right supplier, a company can be sure of getting high-quality and reliable induction furnaces that cater to their specific needs. This is where the expertise of the global leader in the manufacture and supply of induction metal melting furnaces, heat treatment, and forging systems comes in. With their commitment to quality and a proven track record in the industry, they have become a preferred supplier of induction furnaces for various industries. Their comprehensive range of furnaces, heat treatment equipment, and forging systems cater to the requirements of diverse industries, ensuring maximum efficiency and accuracy.
Everything You Need to Know About Efficient Lead Smelting Furnaces
In recent years, the Lead Smelting Furnace (need remove brand name) has become an important tool for companies looking to maximize their metal production efficiency. With its advanced technology and innovative design, this furnace has become a leading choice for businesses looking to increase their lead production capacity.The Lead Smelting Furnace (need remove brand name) is a state-of-the-art furnace that has been designed specifically for the smelting of lead ores. The furnace is capable of processing a wide range of different types of lead ores, including galena, cerussite, and anglesite. This makes it an ideal choice for companies looking to increase their production of lead-based products.One of the key features of the Lead Smelting Furnace (need remove brand name) is its advanced smelting technology. The furnace utilizes a highly efficient smelting process that is designed to maximize the amount of lead that can be extracted from the ore. This results in higher yields and a more efficient production process overall.In addition to its advanced smelting technology, the Lead Smelting Furnace (need remove brand name) also features an innovative design that makes it easy to use and maintain. The furnace is designed with a user-friendly interface that allows operators to easily control and monitor the smelting process. This helps to minimize downtime and ensure that the furnace is always operating at peak efficiency.The Lead Smelting Furnace (need remove brand name) is also designed to be highly durable and long-lasting. The furnace is constructed from high-quality materials that are designed to withstand the rigors of continuous use. This helps to minimize maintenance costs and ensures that the furnace will continue to operate reliably for many years.Perhaps one of the most important benefits of the Lead Smelting Furnace (need remove brand name) is its ability to help companies minimize their environmental impact. The furnace is designed to be highly efficient, which reduces the amount of energy required to smelt lead ores. This helps to minimize greenhouse gas emissions and reduce a company's environmental footprint.Overall, the Lead Smelting Furnace (need remove brand name) is an excellent choice for companies looking to increase their lead production capacity while minimizing their environmental impact. Its advanced technology, innovative design, and user-friendly interface make it a leading choice among manufacturers worldwide.In recent years, demand for the Lead Smelting Furnace (need remove brand name) has grown significantly, with more and more companies turning to this furnace to help them maximize their lead production efficiency. As a result, the manufacturer of the furnace has also experienced significant growth in recent years.The company behind the Lead Smelting Furnace (need remove brand name) is a leading manufacturer of smelting furnaces and other metal processing equipment. With decades of experience in the industry, the company has established a reputation for producing high-quality, reliable equipment that delivers consistent performance over the long term.One of the key factors that sets the company apart from its competitors is its commitment to innovation. The company invests heavily in research and development, constantly working to improve its products and develop new technologies that can help its customers increase their productivity and efficiency.In addition to its commitment to innovation, the company is also dedicated to providing excellent customer service. The company has a team of highly trained technicians and support staff who are available to assist customers with any questions or concerns they may have about their equipment. This helps to ensure that customers get the most out of their investment in the Lead Smelting Furnace (need remove brand name) and other products.Overall, the Lead Smelting Furnace (need remove brand name) and the company behind it are excellent examples of the kind of innovative, customer-focused companies that are driving growth and progress in the metal processing industry. With its advanced technology, efficient design, and commitment to customer service, the Lead Smelting Furnace (need remove brand name) is setting a new standard for excellence in the industry.